己内酰胺(Caprolactam,简称CPL) 是一种重要的有机化工原料,主要用途是通过聚合生成聚酰胺切片(通常叫尼龙-6切片,或锦纶-6切片),可进一步加工成锦纶纤维、工程塑料、塑料薄膜。
尼龙-6切片随着质量和指标的不同,有不同的侧重应用领域。不同牌号的尼龙-6切片性能不同,加工成型后的PA6被广泛应用在毛纺、针织、机织、渔业和轮胎、工程塑料、薄膜以及复合材料等。
己内酰胺曾是公认的聚酰胺产业链领域中技术含量最高、工艺最为复杂的化工中间体产品之一。其生产原料路线主要是苯、苯酚和甲苯。其中甲苯路径是主要的己内酰胺生产方法。以荷兰DSM公司技术为代表,经过制取环己酮合成环己酮肟,经贝克曼重排得到己内酰胺。己内酰胺产品产量、质量的高低,从一个侧面反映了该国的化工技术水平的高低。
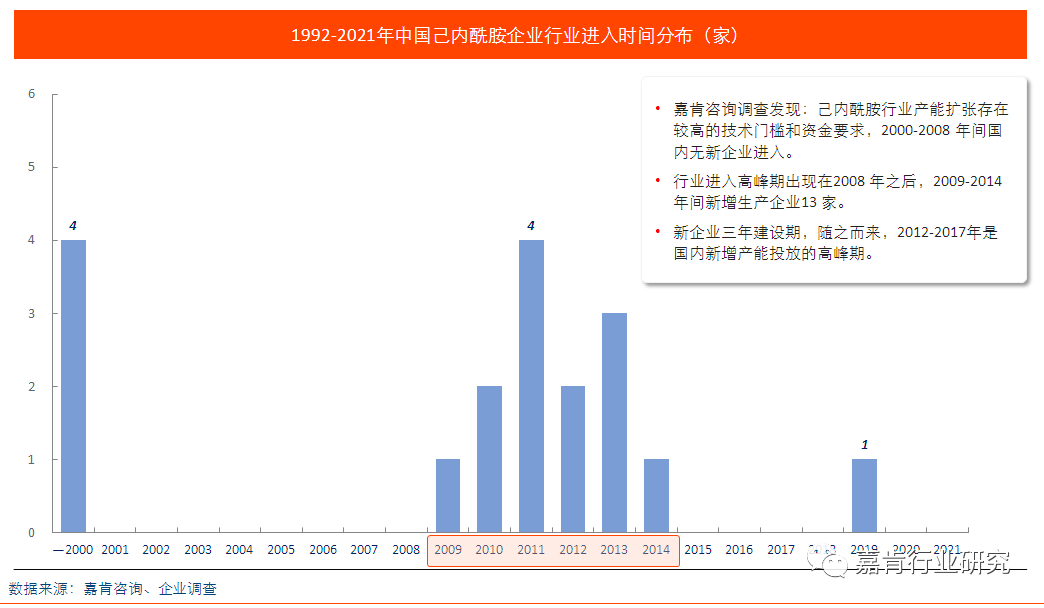
1943年,德国IG公司(巴斯夫公司)开始了己内酰胺和尼龙-6的工业化生产。二战后,德国IG公司的己内酰胺生产技术被公开,荷兰帝斯曼(DSM)公司、意大利斯尼亚(SINA)公司、日本东洋人造丝公司(日本东丽)等利用此技术,开始了己内酰胺的工业生产。
20世纪50年代到90年代初,国内产能主要来自四套采用国内技术的0.5万吨/年生产装置:湖南岳阳化工总厂(巴陵石化)、山西太原化工总厂、江苏南京化学工业公司(南京DSM东方化工)、浙江衢州化工总厂(衢州巨化锦纶)。
1990年,中石化巴陵石化和南京化学工业公司先后引进两套帝斯曼公司HPO法生产工艺技术路线(以纯苯为原料)的5万吨/年己内酰胺装置。
1999年,中石化石家庄化纤引进意大利斯尼亚公司的甲苯法技术,建设了一套生产能力为5万t/a的己内酰胺装置,己内酰胺工业开始逐步发展。通过消化吸收引进的生产技术和装置扩建,形成岳阳(巴陵石化)、南京(DSM东方化工)、石家庄(中石化石家庄炼化)三大己内酰胺生产中心。2001年国内己内酰胺总产能为19.7万吨,表观消费量达44.9万吨,自给率只有34%。
早期国内重化工产业投资对民营资本存在一定的门槛,己内酰胺工业由国有企业主导,发展并不快。2011年底,我国己内酰胺生产企业依然只有四家,总产能为68.5万吨,国内市场需求量升至116.5万吨,自给率为46%。同期,己内酰胺进口量达63.3万吨,进口平均价格为3251美元/吨,同比增长31.5%。
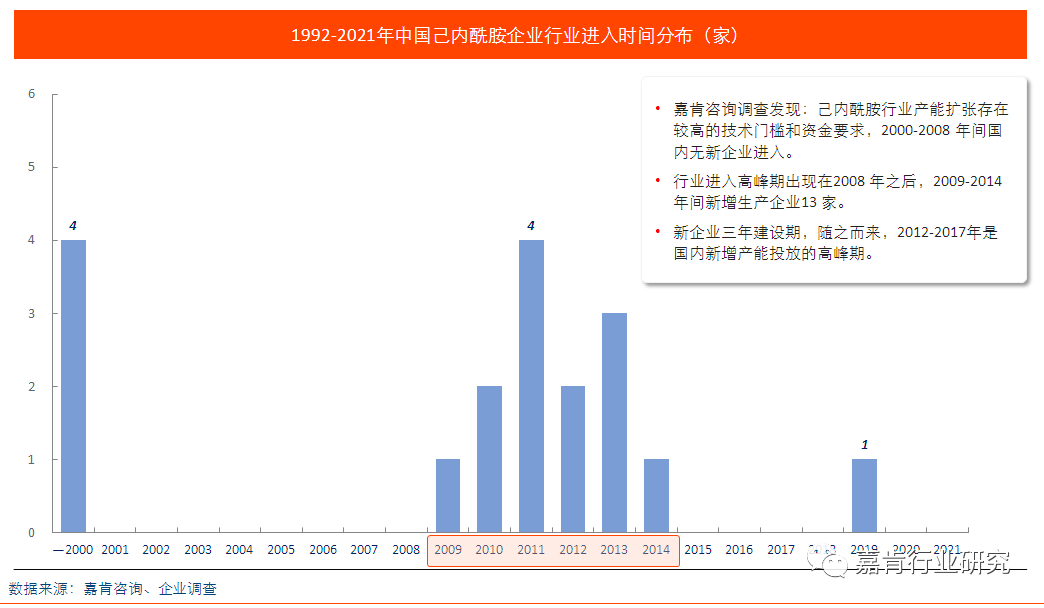
2012年,对国内己内酰胺产业来说,是转折性的一年。
本土企业厚积薄发,终于在己内酰胺的工艺技术和产业化规模方面取得突破性进展。其表现在:三家新入企业己内酰胺生产装置建成并顺利投产,分别是山东海力化工,浙江巴陵恒逸和山东东巨化工公司,新装置年产能为20万吨、20万吨和10万吨。多套超大型生产装置的集中投产,意味着国内己内酰胺产业技术积累,已经跨过了从量变到质变的界点。
山东海力化工是国内第一家进入己内酰胺市场的民营企业,它也是当时国内最大的环氧氯丙烷生产企业,核心技术来源于联合中国天辰工程有限公司和天津大学的自主研发。浙江巴陵恒逸的核心技术来源于合资方巴陵石化——巴陵石化消化吸收帝斯曼HPO技术,通过结合传统的液相贝克曼重排,形成具有自主知识产权的己内酰胺生产技术,资本则来源于母公司恒逸石化。
2012年,山东海力化工、浙江巴陵恒逸、山东东巨化工公司己内酰胺装置相继投产,国内己内酰胺有效产能达到96万吨,同比增长40.1%。当年,进口己内酰胺的平均价格下降21.1%。
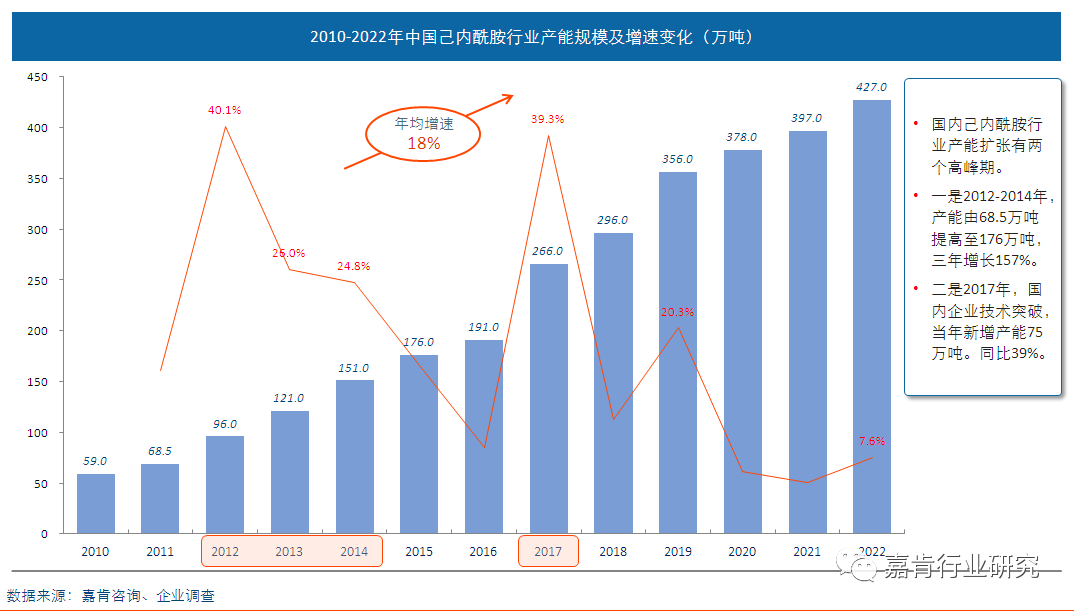
这仅仅只是开始,2012-2017年间,国内有13家新入企业投建己内酰胺生产装置并实现投产,新建产能近200万吨,这种超强度的产能密集投放,改变了全球己内酰胺产业的供需格局,直接后果是国内进口价格不断降低。2016年平均进口价格距离2011年的高位,下降了61%。
本土企业实现工艺技术的突破,行业的产能扩张步伐便不会停止,未来市场价格还将持续下探。由此,己内酰胺产业也由高利润的高技术产业变成低利润的传统制造业,叠加欧美市场己内酰胺需求已趋向饱和,国外老牌己内酰胺生产企业萌生退意,考虑退出己内酰胺业务。
己内酰胺的用途集中且单一,其产业链后段是化学纤维和纺织业。欧美发达国家市场对己内酰胺的需求早在2015年就趋向了饱和。
据商务部统计数据:2011-2015年间,美洲地区己内酰胺的需求量保持在74-77万吨左右,占全球总需求量的比例呈下降趋势,从2011年17%下降至2015 年的15%;欧洲地区需求量维持在104-110万吨左右,所占比重从2011年24%下降至2015年的20%。
全球增量市场在中国。中国己内酰胺需求量从2011年的116.5万吨增长至2015年的209.2万吨,占全球需求的比例从2011年的27%提升至40%,成为全球规模最大且增长最快的消费市场。2020年国内需求量提升至379万吨。
2001年国内己内酰胺总产能为19.7万吨,表观消费量44.9万吨,进口依存度为66%。2020年,国内己内酰胺总产能为397万吨,表观消费量379万吨,进口依存度为7%。
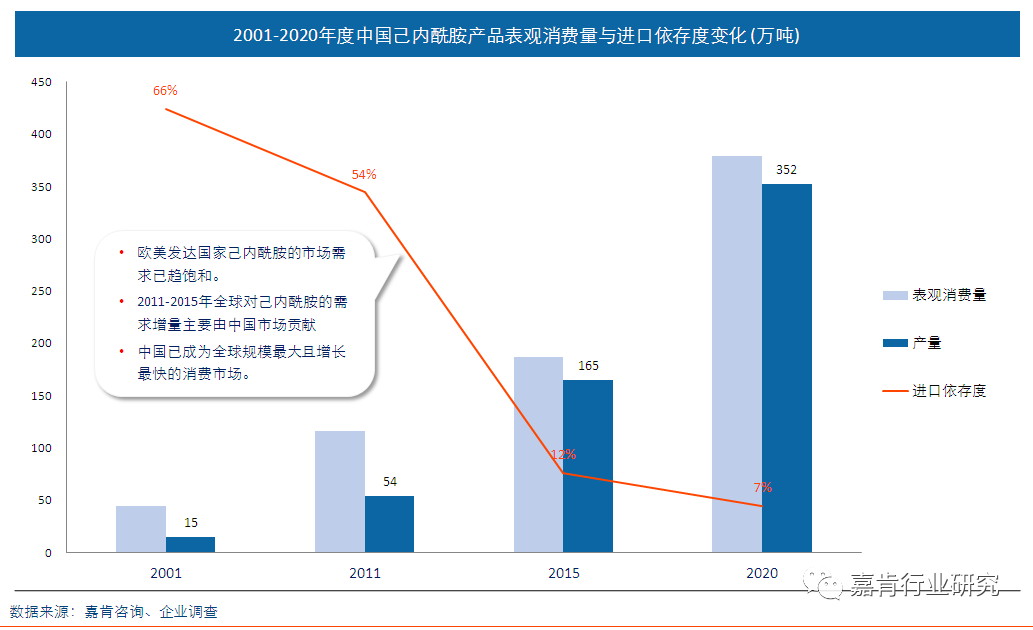
进口主要来源国由以前的欧美发达国家,变成俄罗斯、比利时和白俄罗斯。
依靠本土市场,完全消化了2012-2017年间的新增产能。本土民营企业从新人逐步成长为全球重量级玩家,他们在持续追赶全球领先企业,从落后到赶超,如恒申集团2018年完成收购福邦特公司(Fibrant,原DSM)、恒逸石化拟在广西新增60万吨产能等。固然有民营企业家锐意进取的因素,更重要的是他们依托庞大的本土需求市场,共享全产业链资源,使其投资扩张有更大的容错空间。
这也是国内企业产能扩张的底气所在。日本化工企业在20年前拥有当时全球领先的工艺技术,但其产能扩张的雄心远远不及国内山东企业,非不为,实不敢也。日本企业缺乏纵深广阔的本土市场来滋养其投资扩张,而海外市场的开拓,过度扩张必然要引发本地企业的警惕,面临反倾销制裁,若遇到不诚信不稳定的地方市场,则可能血本无归。
2018年,福建民营企业恒申控股完成对与福邦特控股公司 (Fibrant) 股权收购,恒申收购了福邦特荷兰己内酰胺工厂(福邦特公司)全部股份、福邦特中国南京己内酰胺工厂(南京福邦特东方化工有限公司) 60%的股权,以及世界领先的己内酰胺生产技术、苯酚法环己酮生产工艺、硫酸铵大颗粒生产技术等核心技术和知识产权。由此恒申控股跃升为全球最大、产业链最完整的己内酰胺生产企业。
福邦特是全球最大的己内酰胺生产公司,有66年历史,属于荷兰皇家DSM集团。恒申公司为国内知名的大型纺织企业,曾是福邦特最大的己内酰胺客户。
2013年,恒申与荷兰帝斯曼开展深层次合作,获得了福邦特己内酰胺先进生产工艺的亚洲地区独家技术许可权。
2015年,帝斯曼出于战略转型考虑,需要剥离己内酰胺业务,向CVC股权基金出售己内酰胺65%股权。
2017年,凭着成功的己内酰胺生产经验及相对完善的产业链优势,恒申成为福邦特买家,最终双方达成了收购协议。同年7月,恒申控股年产40万吨己内酰胺及聚酰胺一体化项目,在连江可门港顺利投产,己内酰胺产能位居全球第四。
恒申董事长陈建龙表示,通过此次收购,恒申弥补了多项技术空白,实现了企业对锦纶全产业链全方位的控制。“恒申将以此为契机,利用国际化的视野、全球化的人才,推动整个行业技术进步与转型升级。”
日本住友化学2022年4月发布消息,决定退出己内酰胺业务,将于2022年10月前关闭位于日本爱媛的生产设施。
住友化学从1965年开始在日本爱媛工厂用液相法生产己内酰胺,至今已有50多年的历史。即将关闭的气相法己内酰胺工厂于2003年6月开始运营。
2015年,随着全球(主要是由中国)己内酰胺产能的增长,公司关闭了液相工艺生产线(产能为8.5万吨),专注于气相工艺生产线,该生产线不产生硫酸铵作为副产品。
但近年来,虽然公司继续追求技术改进和成本降低,但住友化学表示,其己内酰胺业务难以确保可持续的竞争力,因此决定于2022年退出该业务。
来源:嘉肯行业研究
原文始发于微信公众号(艾邦高分子):2022年中国己内酰胺行业分析