微结构材料是指内部填充多孔、格栅或蜂窝等不同形式的结构,采用单一材料或多种材料组合作为基体材料的结构化增强材料。微结构材料既是一种结构,也是一种材料,两者之间没有非常明显的界限,具有轻质、高强、可设计、多功能的优点。
汽车工业的迅猛发展对材料的设计开发提出了更高的要求,需要在轻质、高强、节能等方面进行更深入的研究。其中,微结构材料以其优异的性能越来越受到青睐,吸引了国内外众多学者和机构进行研究。
微结构材料在汽车领域的应用越来越广泛:一方面,可应用于车身、底盘、内外饰、动力电池等零部件的结构设计;另一方面,可应用于整车轻量化、安全、噪声、振动与声振粗糙度(NVH)、热管理等诸多性能开发。微结构材料技术的发展不仅颠覆了传统材料开发思维,也给汽车设计开发带来了全新的理念。
微结构材料简介
-
微结构材料
由于微结构材料内部多孔隙,按照孔径的大小可将其分为3类:孔径小于2nm的材料称为微孔材料;孔径介于2~50nm范围内的材料称为介孔材料;孔径大于50nm的材料称为大孔材料。
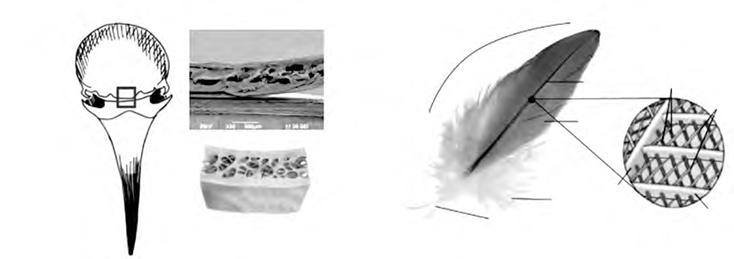
图1 纳米尺度到宏观尺度的微结构材料
图1为从纳米尺度到宏观尺度的各种微结构材料。工程材料从最初的实体材料,发展到桁架结构材料,再到复合材料最终发展为微结构材料,材料形式更加多元化。
2. 微结构材料的原理
自然界大部分生物的微观结构均为空心状、泡沫状或胞状结构。这种结构能在保证受力的同时减轻质量。另外,空心结构也是物质运输和新陈代谢的重要通道。微结构材料质量轻、强度高,自然界中以骨骼、木材等为代表,密度较小,能承受较大的外力。
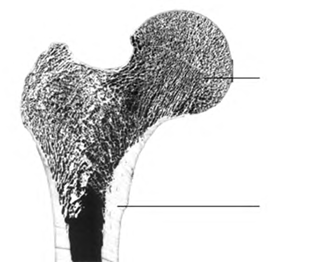
图2 人体骨骼微结构
图2所示为人体骨骼的微观结构,骨松质分布于骨的内部,呈海绵多孔状,由许多针状或片状的骨小梁交织而成,而骨小梁包含数个骨质纤维和矿物颗粒,骨密质包覆在骨松质外层,使骨骼轻质、坚固。
微结构材料的抗振、缓冲、抗弯曲等性能在自然中均有体现。当啄木鸟啄树时,头部以25km/h的速度撞击,却丝毫不受损伤。
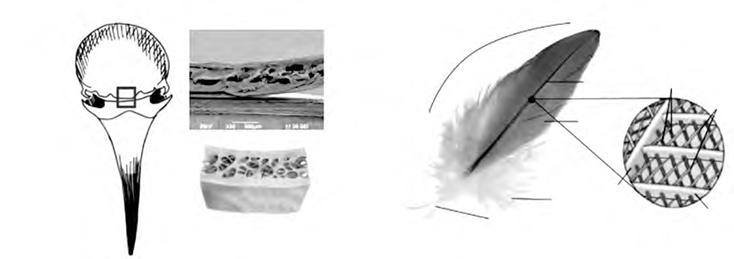
(a)啄木鸟头部微结构 (b)羽毛微结构
图3 啄木鸟及羽毛微结构
图3a所示为啄木鸟头骨及喙骨的微观结构,其头骨和喙骨中包含许多骨小梁,相对于其他动物,啄木鸟的骨小梁具有更大的厚度、更多的数量、更密的间距,使啄木鸟在啄木过程中大量吸收和分散了冲击能量。鸟类在飞行时,羽毛的全部载荷要通过羽轴传递给身体,羽轴却不发生弯曲或折断。图3b所示为羽毛的微观结构,可以发现羽轴包含皮质和髓质,是一种夹芯结构,使羽轴整体具有很高的模量,能有效承载飞行中的羽毛载荷。
负泊松比微结构材料是自然界中的一种特殊微结构材料。贝壳主要由碳酸钙构成,但贝壳的抗压能力是碳酸钙材料的10倍以上。
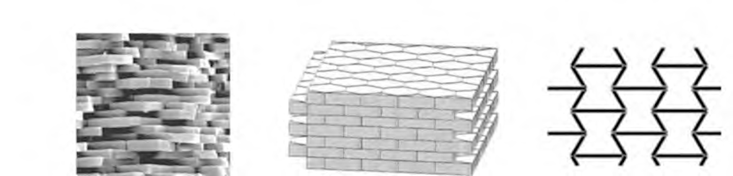
(a)真实微结构(b)简化模型(c)负泊松比模型
图4 珍珠母贝壳微结构
图4所示为珍珠母贝壳的微观结构,贝壳坚硬的原因是其内部结构的有序性使其形成了负泊松比效应,即结构越受压,越往心部聚合,越能产生更好的抵抗压力,使贝壳具有更高的韧性和抗变形能力。
3. 微结构材料的构型
微结构材料按照力学性能可分为正泊松比材料和负泊松比材料;按照结构形态可分为蜂窝结构、胞状结构、管状结构、桁架结构等;按照结构的规则度可分为有序结构和无序结构。
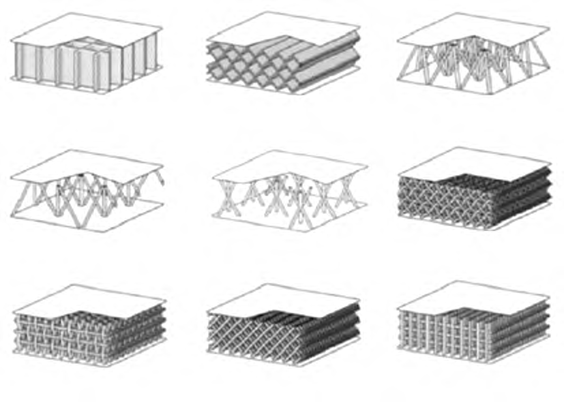
图5 不同夹芯结构形式的微结构材料
在工程应用中,微结构材料通常为夹芯结构,也称作三明治结构。夹芯结构材料由高强度面板与微结构芯材组成,上、下面板较薄,具有一定的刚度和强度;微结构芯材较轻,具有一定的功能性。夹芯结构材料在汽车上已经有成熟的应用,如蜂窝材料盖板等。图5为常见的不同构型的夹芯结构形式。
微结构工程材料种类及特点
除自然界存在的微结构材料外,绝大多数工程材料中的微结构材料由人工合成。结合仿生原理、微结构材料特性,形成了多种不同形状填充、不同特性需求的微结构复合材料,主要种类有多孔金属、多孔陶瓷、泡沫塑料材料、夹芯结构和3D打印微结构材料。不同的微结构具有不同的材料性能,常见的微结构材料(特定牌号)属性如表1所示。
-
多孔金属
多孔金属材料由金属基体和大量孔隙组成,又称多孔泡沫金属,主要的制备工艺有粉末冶金法、纤维烧结法、熔体发泡法、熔体吹气法和渗流铸造法。相对于普通金属,多孔金属具有以下3个方面优点:
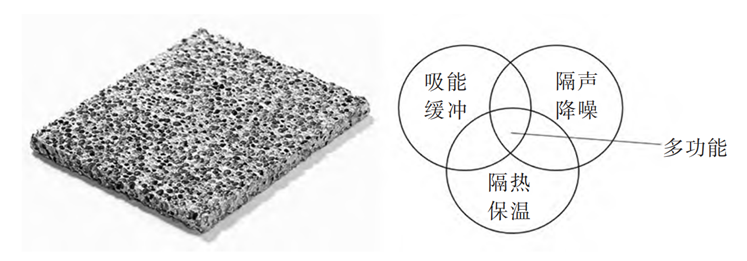
图6 泡沫铝结构及其性能特点
图6所示为泡沫铝材料的结构及其性能特点示意,在多数场合下,多孔金属同时起到强度支撑的结构性作用和吸声、隔热的功能性作用。
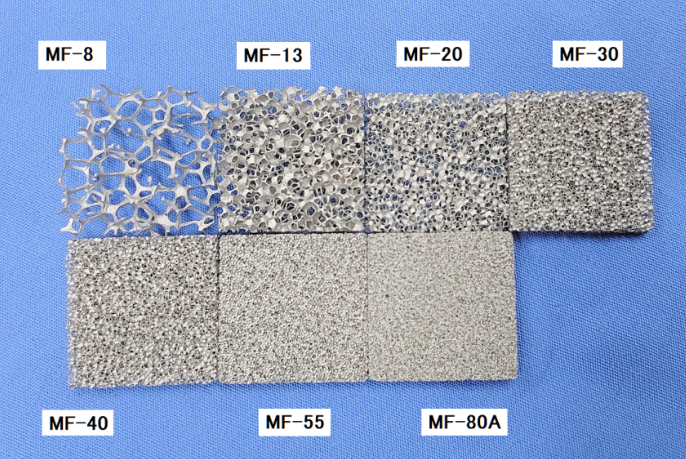
图源:NAGAMINE MANUFACTURING Co.,Ltd.
目前,多孔金属主要应用于吸能、减振、吸声等方面,与多孔陶瓷相比,多孔金属具有抗振、加工性好、导电/导热性好的优势,与泡沫塑料相比,具有强度高、耐热、可回收利用的优势,同时具备结构材料、功能材料的特点,未来在汽车领域的应用潜力巨大。
2. 多孔陶瓷
多孔陶瓷是一种具有可变孔径、高孔隙率的陶瓷材料,以刚玉砂、碳化硅等为原料,经过成型和高温烧结而成,主要的制备工艺有颗粒堆积烧结法、添加造孔剂法、有机泡沫浸渍法、发泡法等,不仅具有耐高温、耐高压、抗酸碱的特性,还具有可控孔结构、高开孔孔隙率的优点,图7所示为一种多孔陶瓷的结构示意。
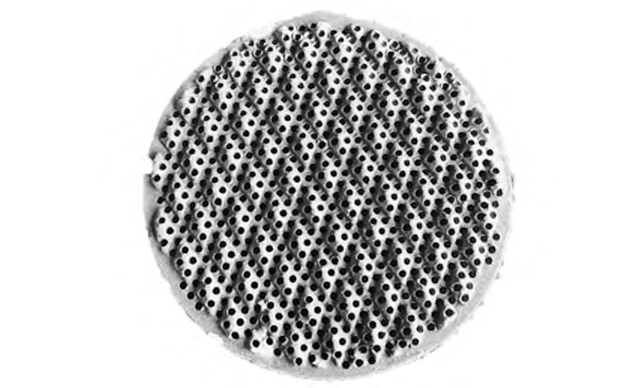
图7 多孔陶瓷结构
目前,多孔陶瓷已在过滤分离、排气消声、电解隔膜等领域广泛应用,另外在吸声减振、保温隔热等方面具有一定的应用潜力。
多孔陶瓷应用于隔膜材料
3. 泡沫塑料
泡沫塑料是工程中最常见的微结构材料,原料为聚氨酯、聚氯乙烯等,通过发泡方式制成,主要的制备工艺有挤出发泡成型、模压发泡成型、注射发泡成型、浇注发泡成型。具有密度小、吸能好的优点。常见的泡沫塑料分类及作用如表2所示,目前,泡沫塑料主要应用于汽车的隔声件或减振件,在白车身及内外饰领域有广泛的应用。
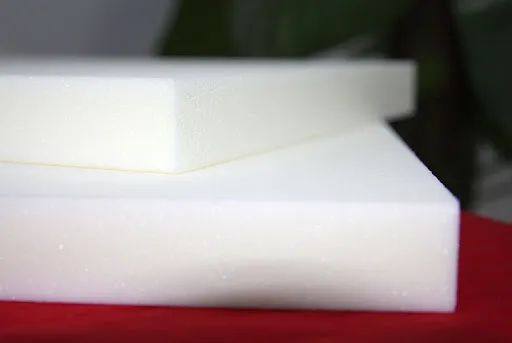
PMI泡沫
4. 夹芯结构材料
夹芯材料是由高强度面层与轻质芯材组成的一种结构材料,又称三明治结构材料。表层厚度薄,有一定的刚度和强度,芯材质量轻、抗弯和抗压性能较好。此外,夹芯结构材料还能够进行隔热或传热,对噪声和振动有抑制作用。
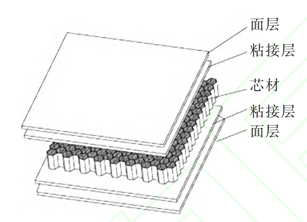
图8 夹芯结构材料示意
图8所示为夹芯结构材料的示意,其中,面层材料可采用玻璃、金属板、塑料板、纸板等,芯材可采用泡沫夹芯、波纹夹芯、木芯夹芯、蜂窝夹芯、桁架夹芯等。
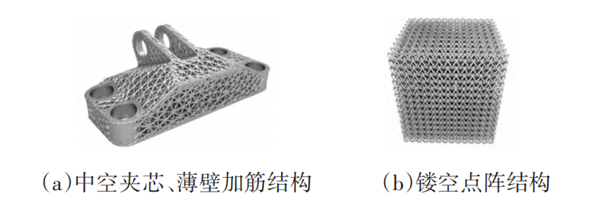
图源:保定维赛新材料
根据不同零部件需求,面层和芯材可进行组合,以获得不同的性能。夹芯结构材料具备高刚度、高强度、轻量化、吸热、隔声等优点,已经广泛应用于汽车零部件。
5. 3D打印微结构材料
3D打印技术是一种以数字模型为基础,运用粉末或丝状材料,通过逐层打印、叠加增材的方式来制造零件的技术,具备精度高、效率高、个性化的优点,能够制造传统工艺无法成型的结构。
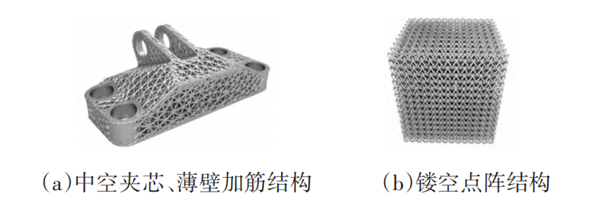

图9 3D打印实现微结构设计制造
如图9所示,3D打印技术可通过多种途径完成有序微结构材料的设计和制造,以获得特定的稳定性能。随着材料-结构-功能的同步设计概念逐步成熟,3D打印技术将与微结构材料设计开发完美融合,实现更大的突破。
微结构材料在汽车上的应用
众多主机厂和科研机构在汽车安全、NVH、热管理等方面就微结构材料开展了大量研究,充分展示了其在产品性能和功能提升方面的巨大潜力,部分技术已实现应用。
-
在汽车安全中的应用
相比于传统实体材料,微结构材料内部存在拓扑微结构,使微结构材料具有优异的能量吸收特性。当微结构受到冲击载荷作用时,内部孔隙使冲击波在微结构内传播的过程中产生折射和反射,冲击波逐渐衰减,能量逐渐被耗散,最终达到吸收冲击能量的效果。
微结构优化了材料的应力-应变曲线,减小了碰撞时的加速度与侵入量,整车安全性能得到提升。因此,微结构材料优异的吸能特性可应用于车辆安全件中,如保险杠横梁、B柱、发动机舱盖等,提升正面碰撞、侧面碰撞以及行人保护性能。
1.1 正面碰撞应用
在汽车正面碰撞过程中,保险杠横梁及吸能盒是重要的吸能部件,尤其是低速碰撞下,能够降低汽车的损毁程度。在防撞梁及吸能盒中填充泡沫金属、负泊松比等微结构材料,能够大幅提升吸能性能,奥迪A8车型在前保险杠防撞梁中应用了泡沫铝。
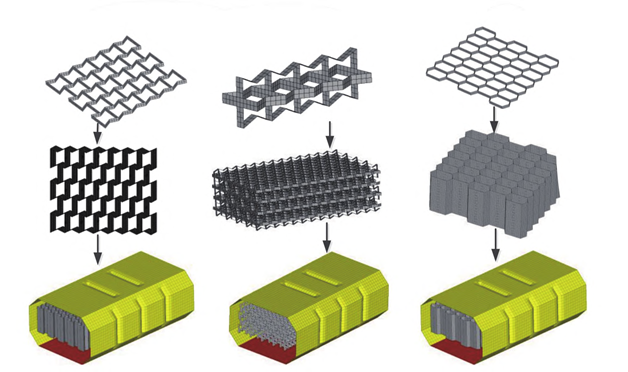
(a)二维负泊松比吸能盒(b)三维负泊松比吸能盒(c)蜂窝吸能盒
图10 3种不同微结构填充吸能盒
图10所示为国内某车型研发的负泊松比微结构材料填充的吸能盒,正面碰撞时,能够明显降低冲击力峰值,提升正面碰撞的安全性,在同等吸能性能下,压缩位移最大可减少24%。同理,在前纵梁、后纵梁中也可以填充微结构材料提升吸能性能。
1.2 侧面碰撞应用
在汽车侧面碰撞中,B柱及其加强板是主要的吸能部件,侧面碰撞变形空间较小,可在钣金空腔内填充微结构材料,在很小的变形范围内吸收大量能量。
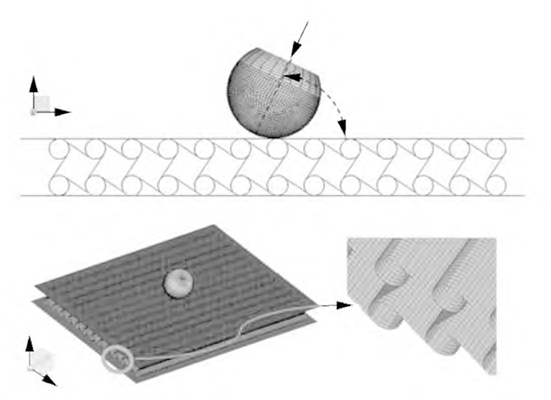
图11 泡沫铝填充B柱及碰撞效果对比
图11所示为某SUV车型泡沫铝填充B柱,在同等的冲击载荷下,泡沫铝填充式B柱结构的碰撞载荷效率更高,为原型车B柱结构的1.16倍。泡沫铝的填充还能提升整车的刚度和NVH性能,进一步提升整车的安全性与舒适性。
1.3 行人保护应用
发动机舱盖是行人保护的关键部件,通过夹芯结构设计,可有效降低行人头部碰撞所受伤害。
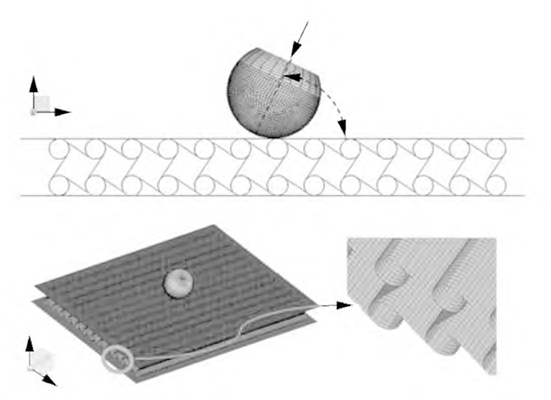
图12 蜂窝夹芯结构发动机罩微结构示意
图12所示为某车型开发的一种新型发动机罩,包含上蒙皮、蜂窝芯材、下蒙皮。试验结果表明,多孔蜂窝芯材的存在使行人头部碰撞HIC值降低22.3%,且延长了碰撞时间,有效减少了二次碰撞伤害。
2. 在汽车NVH中的应用
微结构材料内部具有大量的互相贯通且向外敞开的微孔,当声波入射时,会激发微孔内部空气振动,振动能量转化为热能,使得声能不断减弱。与一般隔声降噪材料相比,在微结构材料中的声波会多次进行反射和折射,使传播路径增大,声能消耗量提升。微结构优化了材料的吸声系数与的NVH性能。微结构材料的特殊结构使其具有优异的吸声、隔声、减振特性,可应用于车辆声学包中,如吸声棉、蜂窝板、泡沫塑料等,显著提升汽车NVH性能。
2.1 多孔泡沫材料吸声减振应用
用于吸声减振的泡沫材料主要包括多孔泡沫金属、泡沫塑料和多孔泡沫陶瓷。多孔泡沫金属材料在低频域具有较高的吸声特性,泡沫塑料、泡沫陶瓷在高频域具有较好的吸声特性。
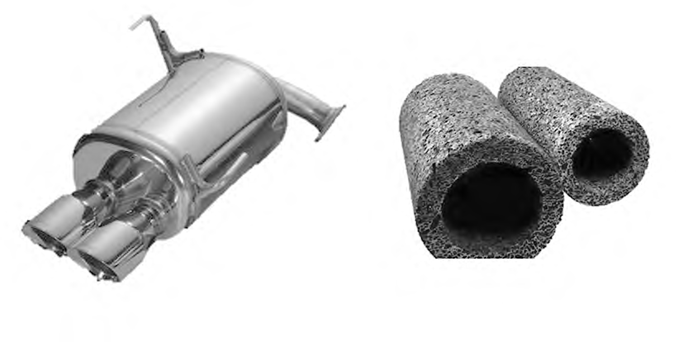
图13 泡沫铝填充的汽车消声器
图13所示为国外某车型采用泡沫铝填充的汽车消声器,可以适用于温度为600℃的尾气降噪,降噪效果为阻抗型消声内芯、并联共振式消声内芯消声器的23倍,质量减轻约1/3;泡沫塑料大量应用于座椅、气囊中,提高缓冲性能;多孔泡沫陶瓷应用较为单一,目前主要用于消声器等高温、高频噪声区。
2.2 多孔纤维材料吸声减振应用
多孔纤维材料也是用于吸声减振的重要材料,吸声减振性能与材料的纤维孔隙结构有关,如纤维的粗细、材料密度、孔隙率等。纤维多孔材料一般作为填料或直接作为吸声材料制成汽车声学包。汽车内饰中大量使用纤维材料声学包,如顶棚、仪表板、门板、前围的吸音棉。
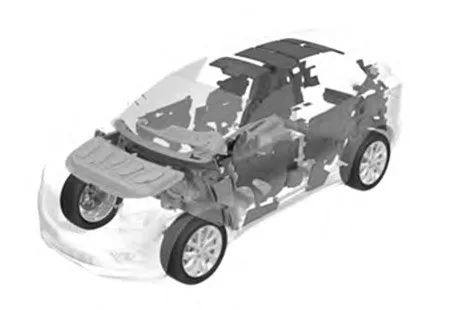
图14所示为整车声学包的示意,多数由多孔纤维材料或多孔纤维材料与泡沫材料复合制成。
玄武岩纤维是一种新型纤维,吸声及耐热性远大于玻璃纤维,特斯拉ModelS的保险杠采用玄武岩纤维制成,减振缓冲效果良好;金属纤维材料高频吸声能力优异,奥迪、大众等车型都将其用作汽车消声器芯。未来,单一的纤维已无法满足NVH要求,复合吸声纤维材料的应用将越来越广泛。
3. 在汽车热管理中的应用
微结构材料的内部微孔分为通孔和闭孔。闭孔结构能够抑制气体在夹芯中流动,从而减小对流和热辐射作用,因此,闭孔材料具有优良的隔热性能;反之,通孔材料有较小的流阻和较大的换热面积,可以提高夹芯内气体与骨架的对流换热效果,因此,通孔材料具有优良的散热性能。
微结构优化了材料的热传导系数,结合不同应用场景,实现隔热/导热的合理应用。微结构材料独特的热学性能使其在汽车热管理中得到大量应用,如动力电池、内饰件等。
3.1 座舱的热管理应用
汽车座舱的保温隔热一直是新能源汽车节能降耗的关注重点,顶棚、地毯等零件覆盖面积大、用户感知强,是座舱进行保温隔热的关键。
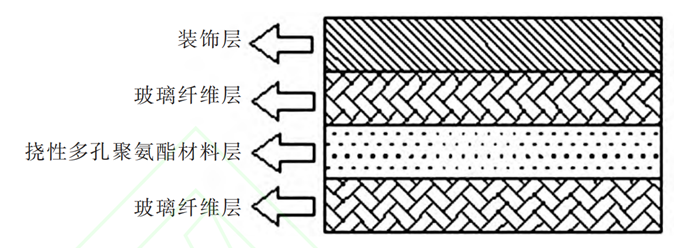
图15 某车型汽车顶棚结构
图15所示为某车型保温隔热顶棚,采用多层隔热材料,并优选导热系数小且反射热波能力强的材料制成复合隔热材料,热流透过率减少10%以上。
3.2 动力电池的热管理应用
锂离子电池在特定条件下存在燃烧或爆炸风险,气凝胶在解决这一问题上有很大的潜力。
图源:中科润资
气凝胶是一种内部网络结构充满气体,外表呈现固体状的多孔材料,是目前密度最低的固体材料,首先在航空航天领域应用。与传统隔热材料相比,气凝胶导热系数极低,在同等隔热条件下,仅为传统材料的1/5~1/2,可有效阻隔电芯在大功率充放电时产生的热量扩散,可在电芯发生热失控时有效隔热,可在电芯燃烧时达到A级阻燃延缓火势蔓延,符合新能源汽车及动力电池更薄、更高效的保温隔热要求。
通用别克微蓝车型在国内首次搭载气凝胶技术,小米SU7也采用了气凝胶进行电池防护。
SU7电芯两个侧面铺设了0.6m² 气凝胶,最高可抵抗1000°C的高温
参考资料:微结构材料及其在汽车上的应用,朱一男等
原文始发于微信公众号(艾邦高分子):微结构材料及其在汽车上的应用