在 20 世纪 60 年代后期以及整个 1970 年代和 1980 年代,热塑性胶带被用于制造各种复合材料部件和结构,特别是在军事和国防应用中。
不难看出热塑性胶带的吸引力。作为 UD带,它们可以应用于许多受力结构,它们是可熔融加工的,并且可以通过压模成型(即热压罐外)或压缩成型(图 1 和图 2)轻松快速地进行固结。它们提供了热固性材料无法比拟的韧性,而且与热固性预浸料不同,它们可以在室温下无限期储存。
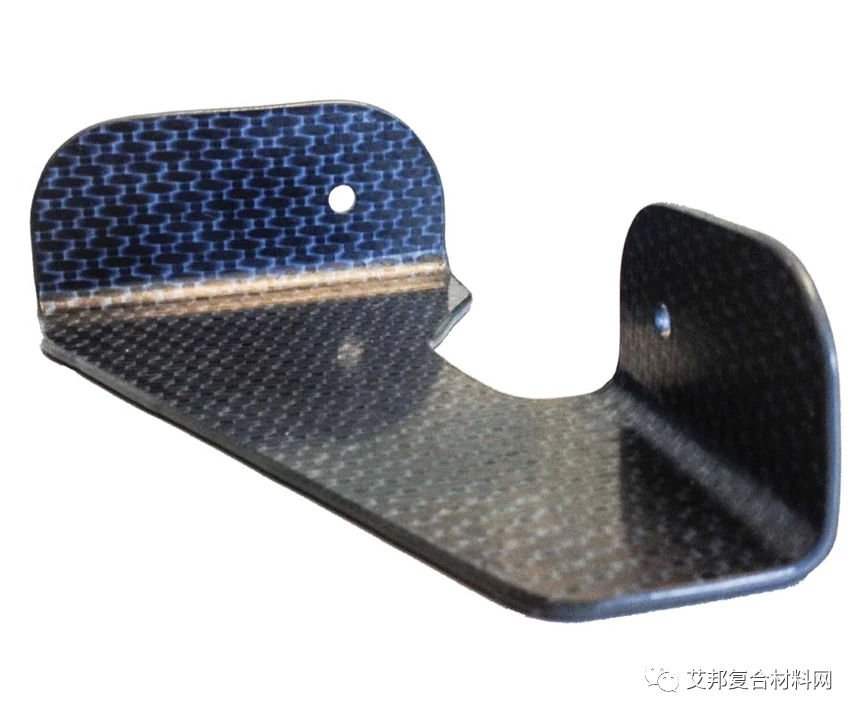
图 1:CFRTP:从支架到大零件
该夹子由 TenCate 提供的编织碳纤维热塑性材料模压而成,象征着该材料在航空航天应用中的潜力。现在正在努力将增强热塑性塑料用于大型、重载的航空结构。
资料来源:TenCate Advanced Composites
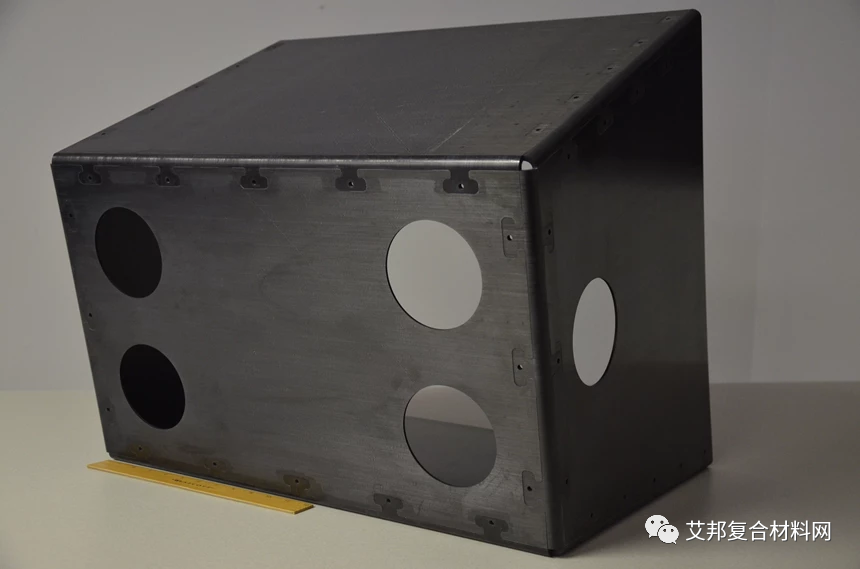
图 2:可行的工艺:冲压成型/模压成型
大多数用热塑性胶带制成的零件都是使用冲压成型或压缩成型制造的,这提供了相对较短的循环时间。此外,热塑性塑料可以焊接,从而简化并加快组装速度。航空航天应用中最常用的热塑性塑料是 PEEK 和 PEKK。
资料来源:Tri-Mack 塑料
然而,随着 20世纪90 年代国防开支的减少,尤其是在美国,人们对热塑性胶带的兴趣和应用也随之减少。杜邦(DuPont)、菲利普斯石油(Phillips Petroleum)、埃克森美孚(Exxon Mobil)、巴斯夫(BASF)和帝国化学工业 (ICI) 等曾在热塑性塑料胶带开发方面投入巨资的供应商退出了该业务。这并不是说热塑性塑料胶带的开发停止了,而是在热固性复合材料(包括热固性胶带)的开发正在加速的时候,热塑性材料带的发展明显放缓。这最终导致后者在波音 787、空客 A350 XWB 和其他商用飞机的大型航空结构中得到应用。
艾邦建有复合材料产业交流微信群,欢迎产业链上下游朋友识别二维码,从公众号底部菜单加入群内交流探讨!
快进到 2018 年。商业航空航天界正在展望未来,下一个预计将消耗大量复合材料的大型飞机项目很可能是波音公司的新中型 (MOM-middle of the market) 飞机,旨在取代其 757。波音 737 和空中客车 A320 的重新设计也即将到来,这些窄体飞机是全球商业航空业的支柱。
在 787 和 A350 XWB 上使用复合材料的材料和工艺经济性与 MOM、737 和 A320 不同。最大的区别是速度。尤其是 737 和 A320,它们是商业航空领域目前最接近商品的产品,这意味着它们的制造速度越快,原始设备制造商的利润就越高。
737 和 A320(以及任何替代它们的机型)的目标产量是每月 60 架或更多,即每天两架飞机。在热压罐中固化的热固性复合材料目前不太适合这种高容量需求。这就是热塑性胶带重返制造业的原因,它们具有热固性材料无法比拟的循环时间、材料储存、韧性和可回收性优势。
如今,它们已被用于制造更小的零件和子结构,包括用于将机身蒙皮连接到桁条和框架的角片和支架。它们被用于小型飞机的许多结构,包括尾翼、机翼和公务机的其他部件。此外,由于热塑性塑料的韧性和耐腐蚀性,石油和天然气行业已经接受了热塑性材料,汽车行业也被其对大批量制造和可回收性的适应性而被吸引。那些在商用机身中使用热塑性塑料的人面临的最大问题是,它们在高负载飞机结构中是否可行?
热塑性塑料专家 TenCate Advanced Composites USA Inc.(美国加利福尼亚州摩根希尔)的首席技术官 Scott Unger 在热塑性塑料领域工作了 30 多年,他说:“热塑性塑料的增长正处于拐点。摆脱热压罐、降低成本和简化零件组装的能力是重要的驱动因素。”
就本文而言,热塑性胶带由宽度达 12 英寸/305 毫米单向排列的碳纤维丝束组成,预浸有热塑性树脂。在航空航天和其他高性能应用中最常用的树脂是以下高性能热塑性塑料:聚醚醚酮 (PEEK)、聚醚酮酮 (PEKK)、聚芳醚酮 (PAEK)、聚醚酰亚胺 (PEI) 和聚苯硫醚 (PPS)。一些制造商提供预浸有商品热塑性树脂的胶带,例如聚酰胺 (PA)、聚丙烯 (PP) 等,但这些通常被认为不适用于大型航空结构。
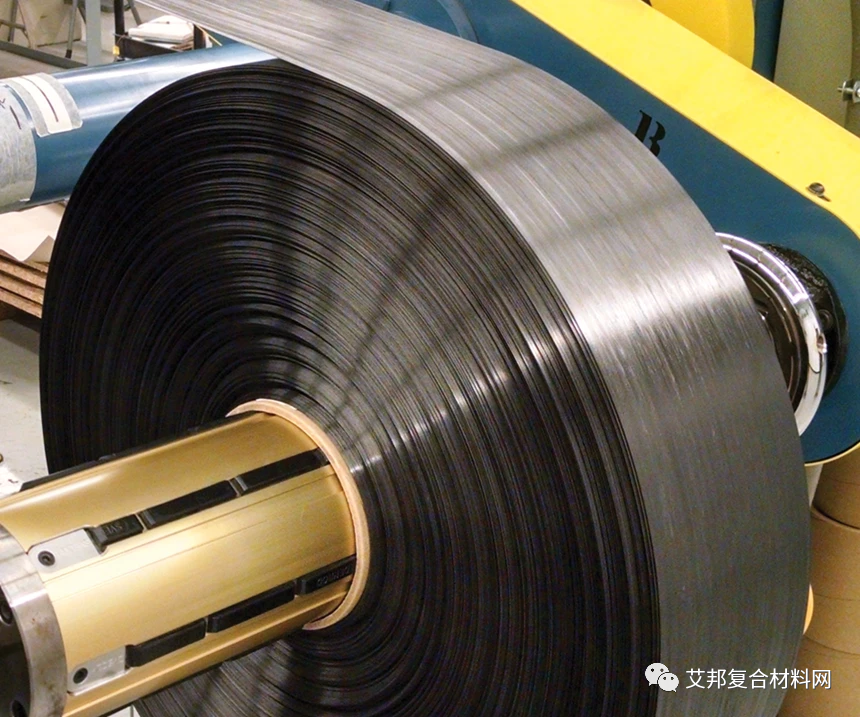
热塑性胶带:曾经和未来的航空材料?
此处显示的热塑性胶带在预浸后缠绕在卷轴上,早在20世纪70 年代和 80 年代,就广泛用于复合材料制造,尤其是军用飞机应用。但随后它们的应用停滞延迟了材料的开发,使它们落后于热固性胶带。然而,热塑性塑料的吸引力,特别是对潜在的高压釜外航空航天应用的吸引力,重新点燃了人们的兴趣和产品开发。
资料来源:Barrday Composite Solutions
对于航空航天工业,最有前途的材料是 PEEK 和 PEKK。“总的来说,这两种聚合物都具有出色的高温性能、良好的韧性和耐化学溶剂性,以及低吸湿性,”预浸料供应商 Barrday Corp.(美国马萨诸塞州米尔伯里)热塑性塑料产品经理 Mike Buck 说。“PEKK 还提供更高的 Tg,以提高耐温性,并降低了加工的熔体温度。”
航空航天制造商 GKN Aerospace Fokker(荷兰 Hoogeveen)的研发总监 Arnt Offringa 表示,PEKK 能够提供与 PEEK 相当的性能,但在较低的熔融温度下加工,使其成为未来商业机身应用增长的首选。
热塑性树脂通常通过基于溶剂或基于水的粉末施加到纤维上。使用的预浸料方法会影响纤维的界面特性,水基工艺比溶剂基工艺产生更光滑的表面。大多数热塑性胶带的纤维体积分数在 40-60% 之间,航空级材料在 50-60% 范围内。
“如果机械性能是主要关注点,并且生产过程具有较长的循环时间和足够的压力和温度灵活性,那么 60% 的纤维体积很重要,”Buck 说。“更高速度或更低压力的工艺,如 AFP/ATL、非热压罐/烘箱加工等,将受益于更高的树脂含量。”
热塑性胶带可以被切割成更窄的胶带或丝束,也可以像热固性预浸料一样被切割成规定的形状来制作坯料,热塑性塑料胶带不像热固性胶带那样有衬纸(背衬)。
热塑性塑料的使用大大改变了制造成品零件的制造步骤。最重要的区别在于,热塑性塑料本质上在室温下是固体,必须加热到熔化温度才能成型。如前所述,PEKK 的 Tg 高于PEEK(160°C 与 140°C);PEEK 的熔体温度高于 PEKK(390°C 与 340°C)。
Solvay Composite Materials(美国佐治亚州阿尔法利塔)复合材料研究和创新小组技术研究员 Jim Pratte 表示,材料的使用取决于应用,并指出 PEKK 是一种共聚物,可以针对不同的温度和结晶度进行定制, 而 PEEK 拥有广泛的数据库,并且结晶速度更快。
这样的温度要求立即使这些材料超过固化环氧树脂或任何其他热固性材料所需的温度。如今,用热塑性塑料带制造零件最常用的工艺是压模成形,将胶带切割成规定的形状,然后堆叠,再放入预热炉中软化和预固结,再将该叠层转移到成型压力机,该压力机通常由匹配的金属工具组成,可在高压 (250-500 psi) 下完全固结和冷却胶带。
“总的来说,我发现与加工热固性材料相比,热塑性塑料的加工通常需要'逆向'的思维过程,”Buck 说。“例如,对于热塑性塑料,通常不想在模具中固化零件,而是形成预热、预加固的层压板,然后使用工具冷却预热的零件。”
原位固结(图 3)不太常见,且仍在开发中,其中通过自动纤维放置 (AFP) 或自动铺带 (ATL) 将切带(丝束)放置在工具上。在该系统中,带头处的高强度激光、热气体或火焰将树脂加热至熔化温度以软化树脂,同时末端执行器施加压力以加固层。最终,这样的系统将在原地进行全面整合,但仍在开发中以供示范。目前,需要进一步固结(高压灭菌或类似处理)以达到孔隙率目标。
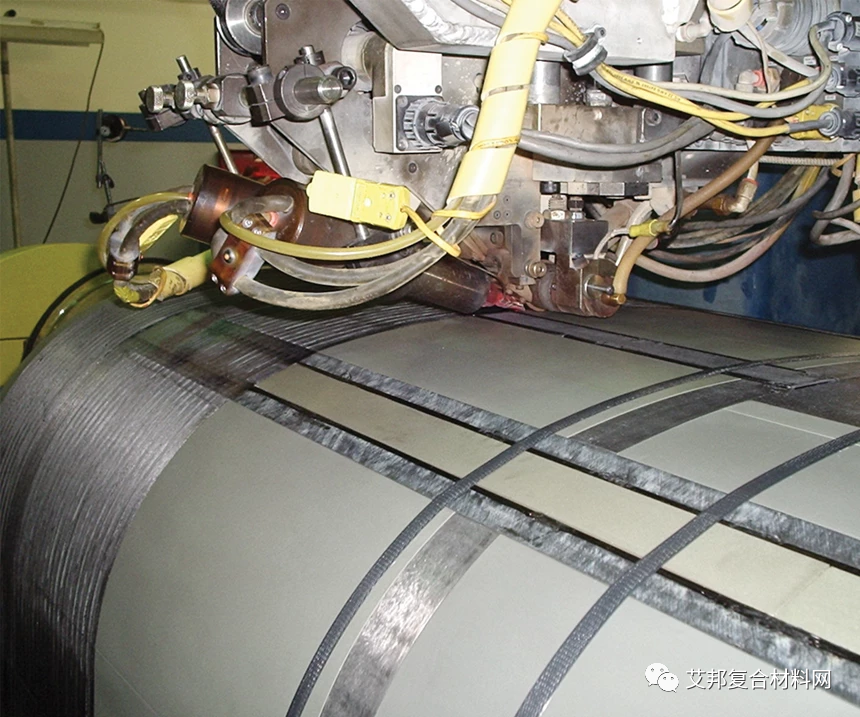
使用热塑性胶带的一种有前途的工艺是通过自动胶带铺设 (ATL) 或自动纤维铺放 (AFP) 进行原位固结。在此过程中,预浸渍热塑性胶带或丝束在胶带头处被加热至熔点 (>300°C),放置在工具上,然后立即由末端执行器加固。虽然此时需要一个额外的高压固结步骤来实现孔隙率目标,但最终,该过程有望在一个步骤中提供 100% 的固结。
Porcher Industries(法国 Eclose-Badinières,法国)的全球和国防业务部门负责人 Pierre-Yves Quéfélec 专门从事热塑性胶带的 AFP,他说该公司与机械制造商 Coriolis Composites(法国 Queven)合作,目标是孔隙率 <0.5%。“这仍然需要热压罐,”他说,“但我们已经开始通过烘箱固化达到这一水平,具体取决于 AFP 的质量。热塑性塑料的高粘度是一个挑战,浸渍的均匀性和一致性也是一个挑战。”
虽然目前尚未被广泛使用,但实现 <0.5% 孔隙率目标的最有前途的工艺可能是连续压缩成型(CCM-Continuous Compression Molding,见图 4)。在这里,连续的胶带通过成型工具,加热和成型材料,并有效地形成一系列形状,包括 T、C、H、帽形和欧米茄型材等。该工艺对于商用飞机的纵梁和框架的制造具有特别的前景。
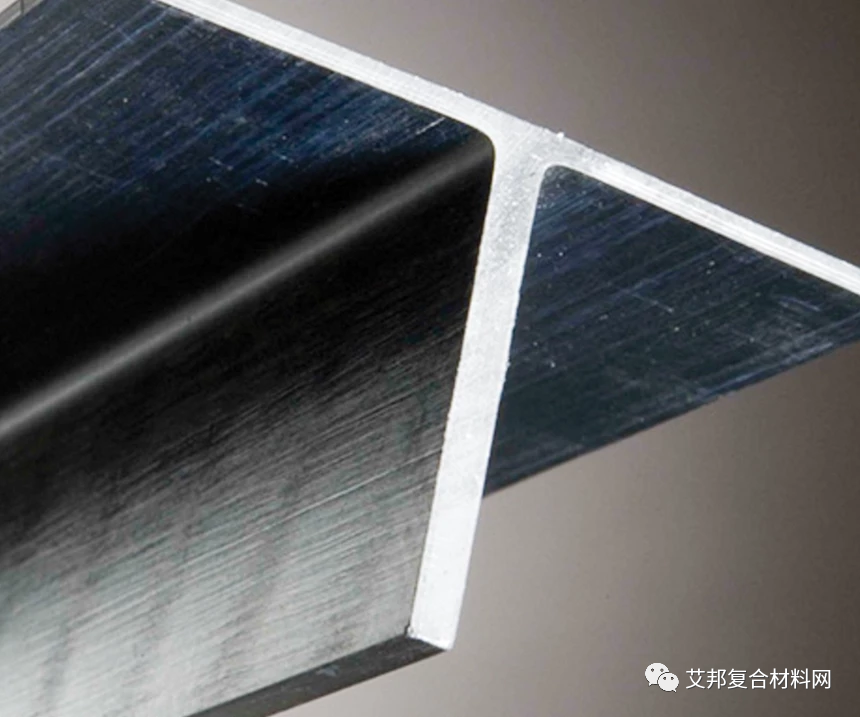
连续压缩成型 (CCM) 并未广泛使用,但被认为是一种高度可行的航空结构制造工艺,其中热塑性带材连续通过一系列成型工具,以制造复合型材,如图所示。CCM 被视为制造飞机机身纵梁和框架的理想选择。
资料来源:xperion
如前所述,热压罐固化是一种选择,对某些人来说是必要的,以确保最小的孔隙率。Offringa 指出,Fokker 更喜欢热压罐,因为它有助于树脂流经纤维,并有助于保持过程控制和一致的零件质量。在热压罐中固化热塑性部件所需的时间通常为 3-4 小时,明显少于固化和固化热固性材料所需的时间。
Solvay 的 Pratte 表示,对于目前使用的大多数热塑性塑料工艺而言,实现孔隙率目标并不困难。“时间和温度消除了大部分空隙,”他说。唯一困难的过程是原位 ATL/AFP,因为时间尺度——在温度下施加压力和巩固胶带所花费的时间——是有限的。“这里的关键点与其说是孔隙率,不如说是胶带中聚合物纤维的浸渍。你可能在胶带中有一些孔隙,但你不能有干纤维,因为原位工艺时间尺度和条件无法弥补这一点。”
一般来说,热塑性塑料,尤其是 PEEK 和 PEKK,很难让人不喜欢。如前所述,它们具有与环氧树脂相似的机械性能特征,但通常比环氧树脂更坚韧。此外,它们也不会放热,并且非常耐腐蚀、耐磨和防火。
热塑性塑料还避免了热固性预浸料的存储和出库时间限制——考虑到冷冻机投资的费用,以及管理预浸料有效期以确定何时使用哪卷预浸料的任务,这不是一件小事。事实上,处理/回收过期材料的成本会大大增加使用热固性预浸料制造零件的成本。
此外,由于热塑性复合材料不会固化和交联,Buck 指出,“热塑性复合材料可以重新熔化/重新加工”。这使得它们相对容易回收。索尔维的 Pratte 指出。“回收是汽车行业的一大推动力,因为汽车的回收量要大得多,而且经济上更具挑战性,”。“如果你不能回收材料,那将成为采用的障碍。” 尽管这对汽车制造商尤为重要,但随着飞机原始设备制造商(OEM)也在考虑生命周期管理 (LCM-Lifecycle Managemen) 和产品报废问题,回收也成为航空复合材料制造中越来越重要的考虑因素。
热塑性塑料还能够以热固性材料无法实现的方式实现部件粘合。它们具有将零件焊接/融合在一起的潜力,这可能会在某些应用中消除对粘合剂的需求。”
GKN Aerospace Fokker 以使用热塑性塑料焊接而闻名,Offringa 表示需要开发多种焊接技术,包括电阻焊接、感应焊接和传导焊接。Porcher 的 Quéfélec 指出 AFP/ATL 是一种连续焊接的形式,据报道,他的许多客户都希望使用焊接将较小的热塑性塑料部件连接到较大的结构中。
随着复合材料在航空航天和汽车领域的使用增加,对自动化的需求将会增加。这也是热塑性胶带的真正机会。“在我看来,这是热塑性塑料大放异彩的领域,”Buck说。
尽管热塑性胶带具有所有优点,但它缺乏热固性胶带的成熟度,因此存在一些挑战。分切和格式化热固性和热塑性胶带的Web Industries(美国马萨诸塞州马尔堡)看到了这些挑战。Web 的研究和技术总监 Grand Hou 说,热塑性树脂由于其韧性,更难切开并满足公差要求。他说,这种材料也有弹性,因此与热固性材料相比,它需要不同的缠绕方式和不同的缠绕控制。
Web 业务开发经理 Jim Powers 指出,热固性胶带的宽度可达 60 英寸/1,524 毫米,可以无缺陷地延伸数千英尺,而热塑性胶带通常最宽为 12 英寸/301毫米,在 700 英尺/17.78米内就有30个缺陷。“热固性材料经历了相同的发展曲线,”Hou说。“我们可能比我们意识到的更接近[重大质量改进]。一旦有一个使用热塑性复合材料的大型项目,你就会看到质量的巨大提高。”
树脂带来的另一个挑战是它的应用。热固性胶带通常使用薄膜形式的树脂进行预浸渍,这使得预浸机能够精确、均匀地涂抹树脂,厚度变化最小。相比之下,热塑性塑料依赖于基于粉末的应用工艺,这种工艺更难控制,并且会产生富含树脂和干燥的区域。这种不均匀性会导致层间孔隙率问题。
Web 的 Powers 表示,溶剂型树脂往往具有更粗糙的表面并产生更多间隙,而水基系统往往更平坦,厚度变化最小且表面更光滑。“较粗糙的溶剂型材料提供更大的表面积,”他指出,“但从缠绕的角度来看,水基系统运行速度更快,并提供更好的材料卷。”
另一个变量是,在室温下,热塑性胶带的特点是不寻常的边界,这会产生一种坚硬的、偶尔不均匀的胶带,容易产生缝隙和裂缝。胶带的厚度也会导致材料波纹,这可能会导致胶带宽度不一致。这会在胶带分切过程中导致后续问题,这依赖于一致的胶带宽度以保持在规格范围内。
此外,与热固性预浸料不同,后者在室温下具有粘性,有助于在铺层过程中层与层之间的粘合。而热塑性塑料是干燥且无粘着性的,需要额外的方法来消除层间滑动,例如点焊。
然而,自动化可能是热塑性胶带的粘性不一定是问题的一个领域。Solvay 的 Pratte 说:“人们过去常常抱怨手糊板又硬又板,但在自动化设备中,太硬的板是一种优势。”
航空航天热塑性塑料复合材料制造商 ATC Manufacturing(美国爱达荷州波斯特福尔斯)的业务发展总监 David Leach 承认,热塑性胶带“通常不如热固性材料稳定,这当然是我们希望看到改进的领域”。Leach 还指出,不均匀的树脂应用会产生树脂丰富的区域,这既有益又有害。他还回应了 Web 的观点,即热塑性胶带中缺陷之间的长度相对较短,并且分切胶带的宽度不太一致。Leach 说,随着自动化程度的提高,这种一致性将是强制性的。
TenCate 的 Unger 说,高胶带完整性对于促进热塑性塑料的使用和弥补制造过程中的限制至关重要。特别是,Unger 指出 AFP/ATL,由于其逐层处理,引入了层间孔隙率的可能性。作为胶带完整性的证明,Unger 引用了 TenCate 热塑性胶带的显微照片(图 5),该照片显示了均匀的层厚度和树脂均匀性。他说,关键是高质量的胶带,空隙率低,是高质量复合材料快速、自动化加工的推动力。具有大量空隙的胶带将需要更长的固结周期才能生产出高质量的零件。
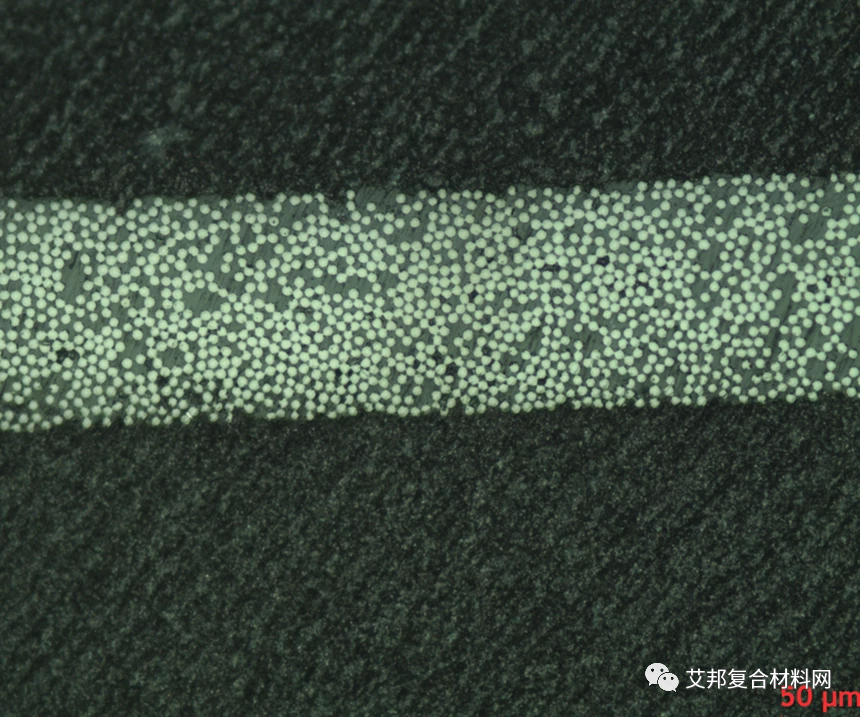
图 5:加工原则:质量产生质量
这张 TenCate 热塑性胶带的显微照片展示了胶带产品的均匀性和同质性。胶带的质量越高,制造商就越容易生产出高质量的零件。然而,使用较低质量的胶带需要更稳健且可能更耗时的过程才能实现良好的整合。
资料来源:TenCate Advanced Composites
最后,还有成本问题。PEEK 和 PEKK 目前比它们与之竞争的环氧树脂更贵,但这种情况有望改变。Offringa 说,“如果随着在高负载主要结构中的应用增加,它像预期的那样强劲增长,成本预计会随着体量的增加而下降。” ATC 的 Leach 对此表示赞同,并指出尽管热塑性胶带已经使用了几十年,但体量仍然很小。“原始设备制造商在复合材料方面拥有丰富的经验,并且倾向于使用胶带,”他说。“从热固性材料转变为热塑性材料的主要驱动因素是成本。我们怎样才能让热塑性零件变得负担得起?”
Porcher 的 Quéfélec 对此表示赞同。“整个价值链……必须重新挑战商业案例。与热固性材料相比,高成本会损害竞争力。技术准备水平(TRL-technological readiness level ) 落后,但正在迎头赶上。”
Barrday 的 Buck 简单地说:“热塑性塑料行业可以使用具有 PEKK/PEEK 性能的聚合物,但价格与 PPS 相当。”
这些真实和潜在的缺陷——缺乏粘性、间隙、波纹、不均匀——造成了下游挑战,尽管这些缺陷是可以控制的,但使热塑性胶带比竞争性替代品更难加工。这反过来又减缓了它们在高性能应用程序中的采用。然而,它们提供的优势是真实存在的,这刺激了对技术和工艺研发的大量投资,以帮助将这种材料推向更大的结构部件。“在过去二十年里,我们完成了基本的创新,”TenCate 的 Unger 说。“未来的主要创新将是工艺和自动化的成熟以及零件制造基础设施的扩展。”
在制造方面,由 GKN Aerospace Fokker 领导的 Thermoplastic Affordable Primary Aircraft Structure (TAPAS) 财团正在为空客开发热塑性飞机机身结构和热塑性扭矩箱(用于尾翼和机翼结构)。正在评估的是一种 TenCate UD 胶带,它包含 Hexcel(美国康涅狄格州斯坦福德)的 AS4 碳纤维和来自阿科玛(法国科隆布)的 PEKK 基体。TAPAS 工作分为两个项目,TAPAS I 和 TAPAS II,后者已接近尾声。Offringa 说,TAPAS 的工作证明了热塑性胶带的潜力,特别是在机身蒙皮、发动机挂架、小型机翼和尾翼结构方面。“材料正在被鉴定,工艺正在被鉴定。这些并不是巨大的零件本身,而是增加尺寸和体积的部件,”他说。展望未来,他说,“其中一家 OEM 可能会取得突破,决定真正转向更大的热塑性塑料部件。”
索尔维的 Pratte 对此表示赞同:“小零件已经起飞,并建立了信心和成熟度。客户开始关注更大的零件。” 为推动这一努力,索尔维和 GKN Aerospace Fokker 于 2017 年初宣布,他们将合作开发热塑性复合材料,而索尔维将成为这家航空航天制造商的首选供应商。
Fundacion para la Investigacion, Desarrollo y Applicaciones de Materiales Compuestos(FIDAMC,马德里,西班牙)也正在评估热塑性胶带在制造机翼和机身结构中的应用,通过高压釜外原位纤维铺设。FIDAMC 的高级复合材料专家费尔南多·罗德里格斯·伦斯 (Fernando Rodríguez Lence) 表示,胶带质量是一个主要限制因素,迫使较慢的铺设速度以弥补胶带缺陷并实现整合目标:“我相信我们的材料供应商将提高胶带质量,提高性能以达到热压罐固化部件相似水平,并解决后处理的需要。”
如果像人们普遍认为的那样,波音或空客决定使用热塑性胶带制造主要结构,则很可能会迅速部署资源来解决胶带质量问题。事实上,在过去 10 到 15 年中,大部分胶带的开发都是由材料供应商和制造商发起和资助的。这样的工作很有希望,但也很有限。OEM 承诺带来的努力和资金将大大改变热塑性胶带的前景。
在其历史上的大部分时间里,热塑性胶带中的碳纤维都没有定型,但随着预浸料为不同的工艺和应用优化材料,这种情况正在发生变化。热塑性浆料的设计不仅可以改善纤维处理能力,还可以改善纤维/树脂的附着力。也就是说,树脂和纤维的成分和性能范围很广,因此,根据纤维、树脂和应用的组合,上浆选项也有很大差异。此外,一些树脂与胶剂不相容。在过去四年中,Toho Tenax America(美国田纳西州罗克伍德)、SGL 集团(德国威斯巴登)和施胶专家Michelman(美国俄亥俄州辛辛那提)推出了针对某些热塑性塑料优化的碳纤维浆料。其他预浸料和胶带供应商也提供热塑性塑料上浆选项,但没有透露具体细节。上浆有两个目的。一是纤维与树脂的附着力。另一个是当纤维被切割或者通过编织或编织机械时,减少纤维摩擦(减少长丝起毛或磨损/断裂)。
索尔维复合材料公司复合材料研究与创新小组技术研究员(Alpharetta, GA, US) Jim Pratte说,“上浆有时是减少纤维摩擦和破损的必要手段。你们的大部分上浆开发都试图在性能和‘可运行性’之间找到最佳平衡,即无扩散、断裂、间隙等。” 预浸料制造商 Barrday Corp.(美国马萨诸塞州米尔伯里)的热塑性塑料产品经理 Mike Buck 说:“上浆考虑对于热塑性预浸料和粉末涂层织物很重要。从历史上看,未上浆的纤维一直是热塑性塑料的主要碳纤维形式。然而,碳纤维供应商开始开发和提供热塑性浆料。” 有人猜测通用热塑性浆料是可能的,但普遍认为这不太可能:“我认为这是一个梦想,”Pratte 说。“我认为这不会发生。当你观察聚合物的表面能时,它的范围太广,无法被一种上浆类型所适应。”
1. 从原文的叙述中可以看出,从2018年开始,聚醚酮酮(PEKK)迅速进入民机复材行业。先是赫氏(Hexcel)与聚醚酮酮(PEKK)制造商法国阿科玛(Arkema)战略联合,研发最新的热塑性(TP)UD胶带。
接着东丽(Toray)于2018年7月收购Cetex公司,将原Cetex公司热塑性胶带中的碳纤维改用自己的碳纤维,同时在原牌号前加上“Toray”:
Toray Cetex® TC1000 Premium
索尔维(Solvay)原本是一家老牌化学公司,它先前收购了民机复材供应商氰特(Cytec),在这种资源的优势下,索尔维推出了APC(PEKK-FC)复合材料。
2. 赫氏(Hexcel)、东丽(Toray)、索尔维(Solvay)三家供应民机复材的公司,通过不同途径都及时推出了自己的聚醚酮酮(PEKK)复材带,这对我国有关行业的发展有着重要启示。
I want to say two words to you: “Thermoplastic tapes”》2018.1.29编译
https://www.compositesworld.com/articles/i-want-to-say-two-words-to-you-thermoplastic-tapes
杨超凡简介:飞机制造高级专家,近年专攻民机复合材料。原航空工业部首批研究员级高级工程师,享受国务院特殊津贴。
原文始发于微信公众号(艾邦复合材料网):杨超凡·聚醚酮酮(PEKK)复材的急速发展