聚碳酸酯(PC)是一种综合性能优良的热塑性工程塑料。如今,全球PC总消耗量超过460万吨,我国亦是PC的生产和需求大国,目前年产量已超过113万吨,预计到2025年我国PC需求量将达337万吨/年。PC生产和需求量虽不及聚烯烃等通用塑料,产生的废弃物亦是冰山一角,但其应用领域广泛,因此废弃的PC材料仍是百亿吨塑料废弃物的重要组成部分。
帝人“Panlite®”聚碳酸酯 图源:帝人
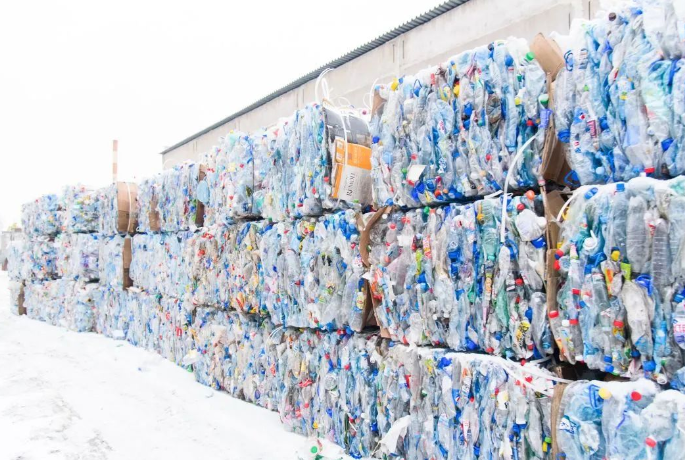
目前采用双酚A(BPA)为原料生产的PC作为主流生产工艺,其废弃物在自然界中缓慢降解,释放出的雌性激素BPA会对生物体造成伤害。将PC废弃物回收利用可以避免BPA对生物体造成不良影响,传统回收方法包括机械回收方法和能量回收法:前者是指将PC废料回收再加工,尽管没有改变PC化学结构但无法保证加工制品性能;能量回收法是指通过焚烧PC废料利用高热量。
鉴于PC机械回收法利用率低,能量回收法环境污染严重,人们关注于化学回收方法研究,该方法可将PC废弃物转化为小分子物质,用于PC合成,具有传统回收方法无法比拟的温和高效、节能环保、产物可持续利用等优点。
对废旧PC的有效处理是发展绿色低碳经济的核心,在此背景下,各国纷纷出台塑料回收和再生政策,构建全球塑料循环体系、实现塑料发展的闭路循环。
本文收集和总结了目前国内外PC化学回收的研究发展状况,以期对PC化学回收技术发展和工业化落地提供借鉴与帮助。
一.国内外聚碳酸酯化学回收技术状况
与机械回收方法不同,化学回收避免了废旧塑料再利用所带来的产品质量下降等问题。长期以来,对PC化学回收研究一直较为活跃,从高能量的热裂解法到具有选择性产物的解聚方式,目前均有较多报道。
Antonakou等将PC化学回收方式进行了归类。主要方式包括热解法、水解法、醇解法、氨解法、氢解法。化学回收原理是通过裂解或解聚PC中的化学基团,将分子量高的PC大分子转化为低聚物或者小分子物质。
其中热解法可根据PC分子基团在不同温度、压力下的稳定性不同,解聚得到种类丰富的产物;
水解法、氢解法使PC分子中羰基断裂,产生酚类物质;
醇解法、氨解法可作用于酯键和芳环-亚异丙基键,除BPA以外,前者会产生附加值较高的碳酸二甲酯(DMC),后者还会产生用于合成聚氨酯(PU)的低聚物。
1热解法
塑料的热解法包括无规降解和链式降解,由于PC在不同的热降解反应条件下的反应机理不尽相同,解聚产物有所差异。
热解法存在明显缺点:一方面,热解法反应时所需温度高,热量消耗大;另一方面,解聚产物的成分较为复杂、回收工序繁琐,PC热解法会产生大量气体并且解聚产物的附加值低,不满足PC解聚的绿色循环发展要求。
鉴于此,科研人员近几年的研究热情不高,而更多关注于对解聚条件温和、产物可控的绿色解聚方法的研究,如水解法、醇解法等。
2水解法
PC的结构与性能相对稳定,然而在特定条件下(如高温、超临界、亚临界、催化剂、微波辐照等)破坏其分子中的羰基结构,可将其水解为小分子产物。
相较于热解法,水解法的解聚温度明显降低,该方法能够减少解聚所需的热量和气体小分子物质的产生。但水解法对解聚反应设备的要求高,需辅以较为严苛的反应条件进行解聚,PC解聚转化率高低不一,产物的组成较为复杂。
因此,如何在保证解聚条件易于操作和PC解聚效果的基础上,兼具转化率稳定性以及产物可选择性的研究是科研人员努力的方向。
3醇解法
PC醇解法主要发生在其碳酸酯键和芳环-亚异丙基键接处,反应得到解聚产物的附加值高,因此该方法得到了广泛的研究。醇解法所用的醇解剂包括:甲醇、乙醇、乙二醇、丙三醇等。
与热解法、水解法相比,醇解法能确保PC解聚产物高效回收利用;此外该方法的解聚条件易于控制、反应过程稳定,符合实际PC化学解聚工业化生产的要求。但采用醇解法进行PC解聚时,催化剂的存在会影响后续分离所得产品的品质,因此需要增加解聚产物催化剂的脱除操作。
4氨解法
近年来,研究人员采用胺类为代表的氮基亲核试剂,在常压温和条件下对PC进行解聚从而获得解聚产物。
近年来,科研人员采用乙醇胺对PC进行氨解,解聚效果明显。周先悦以乙酸乙酯为溶剂,采用乙醇胺对PC在80℃下解聚9h,得到BPA产率为96%。乙醇胺具有较强的亲核性,可在温和条件下对PC进行高效解聚,为PC的氨解研究提供了新的方向。
根据选用的亲核试剂不同,采用氨解法最终生成的解聚产物种类不用,用途各异:与前三种解聚方法相似,该方法可将PC解聚为BPA等小分子物质,可用于PC合成;长链胺的低聚PC,可用于生产不同分子量的PU,这为将PC氨解中间产物用于其他聚合物的合成提供了可能。但该技术尚不成熟,研究较少。
5氢解法
PC分子中具有羰基官能团结构,易发生还原反应,因此科研人员考虑采用氢解技术对PC解聚,这为PC解聚提供新的方法。研究人员开发了多种催化体系用于酯和碳酸酯官能团的还原裂解。
氢解法的反应时间与实验条件(温度、压力、催化剂等)有关,但同样可以实现PC较高的解聚转化率;由于进行反应需要通入H2,因此采用氢解法进行PC解聚,反应设备应具备一定的承压能力。但该方法仍为PC化学解聚回收提供了更多选择。
上述5种方法的研究,为PC的化学解聚提供了多种选择。比较了近年来,不同PC化学解聚方法在反应温度、时间、催化剂加入量和BPA产率等方面的差异,如表1所示。
从表1可以看出5种PC解聚方法中,热解法、水解法无需加入催化剂便可进行化学解聚,但是二者反应温度较高,反应时间较短,解聚产物选择性低BPA产率不佳,故未受到研究者广泛关注;加入催化剂进行解聚反应的3种方法中,尽管氨解法、氢解法催化剂加入量相同,但后者反应耗时长、反应条件较为苛刻,因此氢解法不利PC化学解聚的实际工业化应用;与氢解法、氨解法相比,醇解法兼具解聚条件温和与技术成熟的优点,因此该方法最具发展前景。
PC醇解法解聚所得的BPA产率高,可以有效避免BPA对生物体造成伤害;BPA可作为原料用于合成PC,提高原子利用率,实现PC循环再生,符合当前“双碳”发展理念。
二.解聚催化剂
化学解聚PC时催化剂的存在,可以明显降低反应所需的活化能,从而起到缩短解聚反应时间、提高解聚效率的作用。PC的化学解聚可采用的解聚催化剂的类型多样,主要包括:碱金属氢氧化物、金属盐、强酸、离子液体和低共熔溶剂等,它们可以显著减少CO2等气体小分子物质产生,具有改善解聚速率的效果。
金属盐
在不同化学解聚方法中,呈酸性催化剂可以促进PC水解,不影响化学平衡;呈碱性催化剂主要满足亲核加成-消去机理:即溶液质子转移,破坏化学平衡,从而使PC分子中的酯键发生断裂,最终解聚为BPA等小分子物质。以NaOH为代表的碱金属氢氧化物作为催化剂被广泛应用于PC解聚研究。
碱金属氢氧化物作为PC解聚催化剂,具有价格低廉、易于制得、储存等优势。但是这类催化剂存在使用量大且不能重复回收使用、设备腐蚀严重、产生的三废量大等缺点。因此寻找催化效果好、污染小的催化剂是研究的重点。
综合分析不同类型催化剂的优缺点可以看出,PC解聚工业化的催化剂需要具备以下条件:满足解聚工艺要求、具有催化剂价格优势以及解聚产物带来更多经济效益。
三.发展趋势
近年来,在国家提出“限塑令”、“双碳”目标的政策背景下,科研人员对PC解聚的研究热情高涨,对包括生产和解聚在内PC产品绿色循环产业的发展抱有期待。未来PC废弃物化学解聚工业化落地存在的技术瓶颈及可能突破的方法:
PC废弃物来源及品质问题。目前PC解聚高品质原料(主要包括水桶料、光盘料、车灯料、PC生产装置产生的废机头料等)来源有限,无法满足PC解聚工业化生产的实际需求。对于如PC/丙烯腈-丁二烯-苯乙烯共聚物(ABS)、PC/聚对苯二甲酸丁二醇酯(PBT)、PC/聚对苯二甲酸乙二醇酯(PET)及含多种添加剂或阻燃剂等共混料以及混配料,不利于采用普通方法回收并进行回收再生。
解聚催化剂的选择问题。解聚催化剂应具有反应效率高,催化活性高,选择性高,反应条件温和,易从反应产物中脱除,不影响解聚产物工业化应用特征。未来需要针对PC结构特征开展解聚催化剂的分子结构设计及合成,研究不同中心金属和不同类型取代基对催化剂效率的影响。以期得到多种多配体辅助的金属催化剂,用于解聚反应的研究。
解聚纯化技术的问题。目前醇解法可以实现PC完全解聚,但如何使解聚产物具备工业化应用价值,未来还应关注于解聚产物纯化技术。对于解聚液中的催化剂以及杂质,通过开发探索出绿色、高效、经济的脱除方法,使解聚产品满足达到返回BPA、DMC或DPC装置的要求。这样解聚产品可作为原料用于PC或其他化工产品的生产,实现资源的高效配置和循环利用。
如果解决上述问题,将废旧PC的化学解聚产物用于制备PC产品,既可以实现化工原料合成加工PC制品在各种高端行业的使用要求,又可为PC废弃物的处理提供解决方案。
目前,我国大型炼化一体化企业的发展方兴未艾。依托企业科学、成熟的生产工艺及齐全的配套装置,加快对低成本PC机头料及其废旧制品化学解聚技术的研发,生产出高附加值的解聚产品精制后又可作为PC(或其他化工产品)合成原料,从而紧密联系PC上下游各单元,有利于公司装置提质增效,探索并形成一套完整的绿色循环发展模式。
四.结语
PC的化学解聚方法通常受到催化剂、溶剂、温度等条件的影响,所得产物种类及纯度有所不同。另外,废旧PC的回收成本较高,催化剂还有不易被生物降解、价格昂贵、稳定性差等缺点。
基于上述问题,未来对PC解聚的工业化开发应关注以下方面:
1)开展对于PC解聚机理的剖析、技术效果的提升、其他创新方法的研发等工作。
2)开发合成成本低、高效稳定、环境友好型的催化剂,助推PC醇解法工业化落地。
3)我国的大型化工企业可探索利用现有装置辅助PC解聚,有助于提升现有装置的利用率、减少PC再生过程的复杂工序,实现PC绿色循环再生,助推清洁能源低碳转型。
参考资料:张璐、宋力《聚碳酸酯化学解聚技术的现状与展望》塑料工业,2023.7
原文始发于微信公众号(艾邦高分子):聚碳酸酯化学解聚技术的现状与展望