聚碳酸酯(PC)是分子链中含有碳酸酯基的高分子聚合物,分子结构式见式(1)
PC是几乎无色、玻璃态的无定形聚合物,具有良好的光学性、耐热性、抗冲击性,耐弱酸弱碱以及中性油。高相对分子质量的PC有很高的韧性,但其耐水解性较差,对缺口敏感,耐刮痕性较差,容易受某些有机溶剂的侵蚀、长期暴露于紫外线中会发黄,且不可用于反复经受高压蒸气的制品。
PC根据酯基的结构可分为脂肪族、芳香族、脂肪–芳香族等多种类型,其中脂肪族和脂肪–芳香族PC的力学性能较低,限制了其在工程塑料方面的应用;目前仅有芳香族PC获得了工业化生产。由于PC结构上的特殊性,现已成为增长速度最快的通用工程塑料之一,其综合性能优异,在电子电器、板材容器、汽车工业、医疗器械、防护器材等领域有广泛应用,并迅速扩展到航天航空、光学元件、光电信息等新兴领域。
-
PC生产工艺
目前,PC的生产工艺大致有3种,分别是光气界面缩聚法(又名光气法)、熔融酯交换缩聚法和非光气熔融酯交换缩聚法。3种方法的工艺特点如表1所示。
1. 光气界面缩聚法
光气界面缩聚法的工艺流程如图1所示,反应过程如式(2)所示。
首先,由焦煤或低碳烷烃部分氧化提纯后得到CO,同时将NaCl水溶液电解得到Cl2和NaOH。将生成的CO与Cl2反应制备原料光气,光气与BPA在CH2Cl2溶液中发生界面缩聚生成PC。
此外,电解产生的NaOH可作为该反应过程中的催化剂。得到的PC溶液先通过大量的水洗涤净化,再加入正己烷或甲苯,蒸馏除去CH2Cl2等溶剂后得到PC颗粒,干燥后的PC采用熔体造粒机造粒。反应在常压下进行,缩聚反应后分离的物料、离心的母液、二氯甲烷及盐酸等均需回收利用。
该方法工艺成熟,产品质量较高,对原料纯度无特殊要求,反应设备相对简单且在低温低压条件下即可进行,但在制备过程中残留的氯离子会对产品质量有影响。此外,原料为剧毒物光气,相对危险,同时废气、废水产生量较大。
近年来光气界面缩聚法研发的主要方向为环状齐聚物的开环聚合和后处理工艺。GE(通用电器)塑料、拜耳和三菱化成在后处理工艺中将蒸发和沉析相结合,可借助溶剂和沉析剂除去可溶性杂质,提高提纯效果。
2. 熔融酯交换缩聚法
熔融酯交换缩聚法以苯酚为原料,经界面光气化反应先制备DPC,随后在催化剂(如卤化锂、氢氧化锂、卤化铝锂及氢氧化硼等)、添加剂的存在下,再与双酚A进行酯交换反应得到低聚物,进一步缩聚得到PC产品,反应过程如式(3)所示。
该工艺的生产成本比光气界面缩聚法低,工艺相对简单且产生的废水、废气较少。但该工艺在制备原料DPC时,仍需使用剧毒物光气,产生的含Cl杂质会通过中和反应使碱性催化剂失活,在降低PC性能的同时还会使材料发黄。
3. 非光气熔融酯交换缩聚法
1978年GE塑料首次公开了以Pd为催化剂,使苯酚与CO和O2发生氧化羰基化反应生成DPC,然后DPC在熔融状态下与BPA酯交换生成PC的专利,如式(4)所示。
1980年Romano等首次公开了甲醇与CO和O2发生氧化羰基化反应生成碳酸二甲酯(DMC)的过程,然后DMC与苯酚发生酯交换反应生成碳酸甲苯酯(MPC),MPC歧化生成DPC,DPC与双酚A在熔融状态下进行酯交换缩聚反应制得PC产品,如式(5)所示。
1993年,GE塑料采用双轴式反应器,以CO为原料率先实现了非光气法工业化生产PC,产能为2.5万t/a。
CO2是一种无毒、不燃、生物可再生原料,与CO相比其活性较低,但也可作为共聚单体生产PC。我国的宁波浙铁大风化工有限公司自主研发了以CO2和环氧丙烷为原料的非光气法PC生产工艺,目前的年产量为10万t。日本旭化成公司也开发了CO2非光气法生产PC的工艺流程,如图2所示。
以CO2和环氧乙烷(EO)为原料先合成碳酸乙烯酯(EC),再将EC与甲醇反应生成DMC以及副产物单乙二醇(MEG),随后DMC与苯酚生成DPC,DPC与BPA熔融酯交换生成PC。该工艺是在无水(除冷却水外)环境下进行的,无需使用任何腐蚀性原料。副产物甲醇和苯酚可循环利用,反应过程中可得到高质量PC和高纯度MEG2种产品,没有任何废物和废水的生成。
该工艺不使用有毒物质,原子利用率高,基本无污染,生产过程中多余的原料和副产物还可循环利用,能有效控制生产成本,是典型的“绿色化学”清洁生产工艺,也是未来PC工艺的发展方向。
-
PC研究进展
目前,国家对石油化工企业三废排放的安全环保要求越来越高,对人类和环境造成危害的化工生产工艺与原料将逐步受到限制并最终被淘汰。因此,在PC生产工艺中,对环境无污染、无副产物、投资少、效益好、所得产品质量较好的非光气熔融酯交换技术,必将成为PC生产工艺的发展方向。
但非光气熔融酯交换缩聚法仍存在较高的技术壁垒。该工艺对原料BPA和DPC的纯度要求较高,低成本地生产超高纯度DPC仍存在很大的技术障碍,如能掌握一种相对便宜的DPC生产技术,就能在市场中占据绝对优势。同时,BPA与DPC的熔融缩聚反应虽无需添加催化剂即可进行,但反应平衡常数较低(k<1),必须及时有效地从熔融混合物中清除副产物苯酚,才可提高反应收率。
此外,PC的熔体黏度极高,现有的商用反应器不能用于生产所需相对分子质量的PC预聚体(聚合度约为22~50),因此研发高效的反应器十分必要。
1. DPC的合成
目前DPC的合成技术主要有2种,一种是通过苯酚与DMC反应,另一种是通过苯酚直接氧化羰基化法来合成。
(1) 苯酚与DMC合成DPC
苯酚与DMC合成DPC的步骤如式(6)~(8)所示,该反应在均相或多相催化体系中进行。
首先,DMC与苯酚发生酯交换反应生成MPC[式(6)],MPC再与苯酚反应[式(7)]或MPC发生歧化反应生成DPC[式(8)]。
DMC与苯酚的反应存在着严重的热力学限制,而且会生成副产物苯甲醚。通常通过高温气相反应或带有蒸馏过程的液相反应来提高MPC的产率。
日本旭化成公司研发了一种工业活性蒸馏技术用于生产超高纯度DPC和高纯度的单乙二醇。该装置有2个相互连接的连续多级蒸馏塔,第1个精馏塔以Pb(OPh)2为催化剂用于生产MPC[反应(6)],底温为225℃,顶压为7×105Pa,内部装有筛板,塔板数为80。
反应完成后,包含w=18.2%的MPC、w=0.8%的DMC、苯酚、DPC和催化剂的高沸点混合物从第1个精馏塔底部流出,直接进入第2个精馏塔中用于生产DPC。第2个精馏塔(塔板数=30)的塔身上部安装有2套波纹填料(总塔板数=11),塔身下部采用筛板作为内部构件。其底温为210℃,顶压为3×104Pa,回流比为 0.3。
从第2个精馏塔塔底流出的高沸点混合物中MPC的质量分数为38.4%,DPC质量分数为55.6%,DPC选择性高达98%。2个蒸馏塔顶部提取出的低沸点混合物(甲醇、DMC和苯酚)可循环利用。该装置每小时可生产超高纯度DPC 5.74t,且基本上不含卤素。
(2)苯酚直接氧化羰基化法合成DPC
由CO和苯酚直接氧化羰基化法合成DPC的反应过程见式(9)。因其不需要使用光气被认为是合成DPC的理想方法之一。
Song等以非均相Pd/C催化剂体系为研究对象,比较了Ce(OAc)3/Pd和Bu4NBr/Pd的不同配比对DPC产率的影响:当Ce(OAc)3/Pd和Bu4NBr/Pd的配比较低时,DPC的产量随助剂含量的增加而增加;当配比较高时,DPC的产量趋于平缓,最优条件下,苯酚转化率为37.6%,DPC的产率最高可达26.8%。
2. 反应器的设计
PC的熔体黏度极高,生产过程中若长时间在高温中滞留或旋转,会导致PC出现发黄或变质。
因此,PC反应器的研发主要集中于开发有效的机械搅拌系统。目前,已生产出有自清洁功能的卧式双轴型反应器和卧式双螺杆式反应器,但这些反应器还是难以生产聚合度大于35的PC(中等黏度等级),且需使用大功率电机来旋转双轴,并不节能。
目前,日本旭化成开发了一种利用重力的新型无搅拌熔体聚合反应器。让预聚物沿反应器内垂直安装的导管向下流动,在没有任何机械搅拌的情况下,就可有效去除副产物苯酚。预聚物在导管内流动时内部会有许多气泡,这意味着在此过程中发生了非常有效的表面更新。
该反应器可在较低温度(<270℃)下发生反应制得所需相对分子质量的PC(聚合度约为22~50)。由于聚合温度较低,该装置可用于生产无色、透明、高性能、高纯度的PC,而且利用自然重力代替传统的机械搅拌,大大减少了电力的消耗。
-
PC的市场及发展前景
近年来随经济的飞速发展和新应用的不断扩宽,PC已成为发展最快的工程塑料之一,主要生产商集中在美国、西欧和日本,其中德国拜耳公司、美国GE塑料公司、道化学公司以及日本帝人公司控制着世界PC的生产与市场。
2020年,亚太地区的PC需求量占全球72.6%左右,而中国成了全球最大的PC生产和消费国。随国家政策的大力支持,以及以合资形式引进的PC工艺技术和国内自主研发的生产技术的不断成熟,各大PC生产项目纷纷投建,极大提高了国内PC的产能,使这一产业迎来了新的发展机遇。
PC生产工艺的技术壁垒相对较高,我国起步较晚。2015年以前国内的PC生产装置均为合资企业兴建或技术引进,产能高度集中。宁波浙铁大风化工有限公司年产10万t的非光气法PC装置投产,标志着我国进入了PC自主研发阶段,此后万华化学、四川中蓝国塑新材等企业先后开发出拥有自主知识产权的各种PC合成技术,使我国PC产业发展壮大。
目前,全球的新增产能主要集中在中国,2019年我国的PC产能为166万t,同比增长31.74%,产能利用率为58%。2020年中国PC产能增至244万t/a,产量增至118.5万t。
PC先后被列入国家高新技术产业、重点战略性新兴产业和《中国制造2025》中叙述的十大重点领域。受国家政策的鼓励及国内产能的大量投入,未来国内PC市场必将呈现供大于求的局面,保守预计到2023年中国将有241万t/a的PC产能释放,届时中国PC总产能将接近360万t/a。
和快速增长的PC产能相比,其下游需求却未同步释放。整体来看,PC消费增速乏力,行业进入低速发展期。普通的PC抗冲击性能和耐化学性较差,在很多领域都无法应用,但高端产品的生产技术壁垒较高。国内企业在高速扩产的同时,应加强产品品质的提升,改变低端产品过剩、高端产品缺乏的困境,才能在激烈的市场竞争中不断发展壮大。
PC的三大生产工艺中,非光气法对环境无污染、无副产物、投资少、效益好、所得产品质量高,必将是PC未来的发展方向。目前可通过开发高效催化剂来降低高纯度DPC的生产成本,此外,还可通过设计高效反应器使其适用于生产高熔体黏度的PC预聚体。
我国PC的产能和消费量虽不断增大,但产品普遍为基础料,主要用于包装、薄膜和板材等方面,应用范围较窄、利润较低。而应用于汽车、家电、电子产品等领域的高端产品,仍依赖于合资或外资企业。随产能的进一步释放,供需逐渐接近平衡,PC行业竞争加剧,企业面临着巨大挑战。淘汰环境不友好的技术、降低PC原料的生产成本、调节改善产品性能、开发高性能产品、降低装置能耗、提高装置竞争力、加大国产技术的自主研发力是未来PC行业的发展方向。
参考资料:聚碳酸酯的研究进展及市场分析,张文琴等。
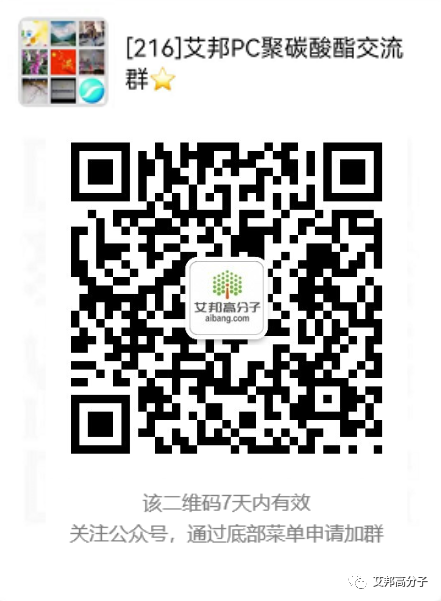
原文始发于微信公众号(艾邦高分子):聚碳酸酯PC的聚合方式研究及市场分析