新能源汽车行业即将迎来磷酸铁锂(LiFePO4 )锂离子电池的“退役潮”,如何处理和利用这些锂离子电池中的废旧LiFePO4 材料,已成为迫在眉睫的问题。
目前废旧LiFePO4 的回收处理方法,包括火法冶金、湿法冶金、直接再生、及电化学再生。
-
1.火法冶金
-
传统的火法冶金回收一般是高温焚烧电极片,将电极碎片中的碳和有机物燃烧掉,不能被燃烧掉的剩余灰分经筛选,得到含有金属和金属氧化物的细粉状材料。该工艺简单,但处理流程长,有价金属的综合回收率较低。
火法冶金领域已有大量改进后的研究成果,其中一些已在工业规模上得到应用。火法冶金回收路线的总体回收率较高,在某些情况下超过50%。
当前火法冶金工艺的主要缺点是Li的结渣,但近年来炉渣后处理领域取得了一些进展。如在火法冶金过程和随后的湿法冶金处理时,通过选择性添加熔渣形成剂,提高熔渣中Li的浓度。
LiFePO4的橄榄石结构非常稳定,不能够在温和条件(低于1000℃)下被碳还原,无法实现Li2CO3的回收。有研究发现,添加Na2CO3,有利于LiFePO4的碳热还原,可将Li的回收率提高到99.2%。
-
2. 湿法冶金
-
传统的湿法冶金主要是用合适的酸对废旧电极材料进行浸出,随后,用不同方法回收所需的金属。废旧LiFePO4湿法冶金回收时,经常用的浸出剂是HCl、H2SO4和H3PO4。
LiFePO4的预处理必须在后续浸出和分离之前,将Fe从+2价氧化为+3价,原因是Fe3+更容易形成沉淀,因此,在浸出过程中通常需要加入氧化剂。
对于LiFePO4材料,已经开发了两种主要的湿法冶金回收策略,包括将Li和Fe溶解成离子形式的传统方法和选择性浸出Li的方法。由于LiFePO4的结构很稳定,传统的浸出过程将消耗过量的酸和碱,以中和溶液。
此外,还需要分离Li+和Fe3+,以回收有价值的Li元素。为了简化回收过程、节约成本,近年来对锂进行选择性浸出的研究成为了研究者关注的方向。
(1)选择性浸出锂
在选择性浸出Li的过程中,必须加入浸出剂和氧化剂。选择的材料不同,Li、Fe的浸出率不同。
-
以H4P2O7溶液作为浸出剂,在浸出过程中,溶解的Fe2+与P2O74-结合,在氧化后形成Fe4(P2O7)3沉淀。该工艺将常规浸出和分离过程合并为一步,最终得到的Fe的浸出率接近100%,而Li的浸出率为97.98%。
-
采用甲酸(HCOOH)作为浸出剂,H2O2作为氧化剂,可制备负极材料Fe2P2O7,证实了选择性提取锂和同步分离Li、Fe和Al元素的可行性。在最佳实验参数下,Li的浸出率可达到98.84%,Fe、Al的浸出率则低于1%。值得注意的是,浸出渣FePO4被灵活地用于再生Fe2P2O7,可以作为锂离子电池的负极材料,并表现出较好的倍率性能和循环稳定性。
-
在室温下添加过硫酸铵[(NH4)2S2O8]后,通过一步氧化浸出反应,就可分离出铝箔、含锂化合物和高纯度FePO4等3种材料,最终Li的浸出率超过98%,且再生LiFePO4的倍率性能和循环性能都较好。
-
空气作为廉价和绿色的氧化剂,也可以用于选择性提取锂。在pH=3.5、空气流速600ml/min、温度为25℃、固液比为10g∶1ml的最佳条件下,Li的浸出率为99.30%,仅有0.02%的Fe和P溶解。此外,空气的还原产物为H2O,不会引入任何杂质。浸出过程中,可以直接从浸出液中得到高纯度的Li2CO3产品,无需净化。
所有的浸出过程都需要大量的酸和还原剂/氧化剂,才能达到预期的浸出效果,酸浓度为1.0~3.0mol/L,还原剂/氧化物的消耗量较高。任何未反应的酸或还原剂/氧化剂,最终都会进入流出物中,并造成二次污染。不同工艺对废旧LiFePO4的浸出结果如图
不同工艺对废旧 LiFePO4 的浸出结果
综上所述,无机酸浸出和离子分离工艺具有较高的浸出率和高纯度金属产品的回收率,但需要控制酸的消耗,浸出过程中的最佳提取参数需要进一步优化。应充分考虑简化回收过程和节约化学品/能源消耗之间的平衡,以实现废旧LiFePO4锂离子电池中不同金属的高效和绿色回收。
(2)提取
将金属离子溶解在浸出剂中后,要从浸出液中获得有价值的产品,即电极材料或前驱体。传统上,浸出液中的金属离子将转化为不溶性氢氧化物或盐沉淀剂;选择性沉淀是一个繁琐的过程,包括分离单个金属离子的一系列步骤。
从浸出液中回收用于合成正极材料的前驱体,通常采用共沉淀法和溶胶-凝胶法。共沉淀法的再生机制包括3个主要步骤:
首先,废旧正极材料中的单一金属在适当条件下,通过无机酸/有机酸溶液浸出;
随后,将选择的共沉淀剂加入上述浸出液中,形成所需的固态中间体;
最后,对获得的固态中间体进行高温处理,以重构晶体,高温烧结后,得到再生的正极材料。
除了共沉淀法外,溶胶-凝胶法也是从溶解正极材料的浸出液制备均匀中间体的一种方法。
溶胶-凝胶法的再生机理与共沉淀法几乎相同,只是共沉淀反应被溶胶-凝胶反应步骤所取代。在溶胶-凝胶过程中,具有丰富配体的螯合剂有助于混合浸出溶液中的金属离子,以形成高纯度和均匀的前驱体,有利于在随后的煅烧过程中制备出均匀分布的纳米颗粒。
3.直接再生
LiFePO4的晶体结构稳定,在过充/过放过程中均不会受到破坏,可采用直接再生技术回收废旧LiFePO4,并省去将活性材料分离和再制造正极电极的工艺。作为一种低成本、节能的回收途径,与湿法冶金方法相比,直接再生具有环保、二次污染少的优点。
可使用功能化预锂化分离器(FPS)的原位电化学过程直接再生LiFePO4电极。FPS通过在商用分离器上涂覆一层薄的富锂材料来制备。该预锂化技术简单,大大降低了正极的再制造成本。
可以按照不同比例复合,设计出双离子电池(DIB)的复合正极材料(LiFePO4/石墨)。这种复合正极能够实现阴离子和阳离子同时参与嵌脱过程,达到LiFePO4和石墨负极的直接再生回收。
直接再生技术被认为是具有经济竞争力和前景的回收方法。少量杂质(如Al)就会显著恶化再生LiFePO4的电化学性能,因此,需要非常仔细地调整工艺参数,确保再生正极的高纯度。
4.电化学再生
电化学法以外部电能作为驱动力,促使废旧LiFePO4发生一系列化学反应,达到材料再生回收利用的目的。
目前,主要思路有两种:通过电解,废旧材料中的部分元素以离子的形式脱出,然后分别回收;对废旧LiFePO4进行补锂,修复再生。使用熔盐电解的方法,可将LiFePO4在正极转化为Fe,在负极转化为Fe3O4,同时,将Li+和PO43-释放到熔盐中,Li的回收率超过95.2%。
另一种是更绿色、低成本的电化学再生方法。该方法主要是在水溶液系统中,通过H型电解槽,构筑低成本的原电池,负极为廉价的锌金属,正极为待再生的废旧LiFePO4。通过放电过程,Li+重新回到废旧LiFePO4。
总结
目前,废旧LiFePO4材料的回收方法各具特色。火法冶金尽管环保压力大,但被大多数用户采用;湿法冶金中,Li和Fe的回收率高,但需要大量的酸和氧化剂;
直接再生在成本、安全性、环境友好性、能源消耗、效率和产品价值等方面具有优势,但在工程化和产业的综合利用方面还有待于进一步验证;
电化学再生凭借绿色、低成本和高效的经济优势,具有很强的竞争力,即便在碳酸锂价格低于4万元/t时,仍有经济效益,但如何适应LiFePO4材料的产业生态,是一个必须解决的问题。
在目前碳酸锂价格高企的情况下,废旧LiFePO4的回收不存在经济方面的压力,因为企业的重点是Li的回收,可解决电动汽车电池退役所带来的问题。
为了实现LiFePO4动力锂离子电池产业的良性发展,Fe、P的回收是非常重要的,迫切需要更多的研究,以构建完整的回收链,并评估回收工艺的可行性及对环境的影响,以促进回收工艺的实用化和绿色化
本文参考资料:锂离子电池中废旧磷酸铁锂的回收、网络等
储能产业交流群
2021年全球电化学储能装机规模21.1 GW。其中,锂离子电池93.9%;铅蓄电池2.2%;钠基电池2.0%;液流电池1.2%;超级电容器0.2%;其它0.5%。到2025年,预计电化学储能增量将达到12GW/年,累计装机约40GW。在储能产业链中,各种电化学储能技术、新材料、先进制造设备、储能配套设施等都迎来了爆发式增长的机会。为促进储能产业行业交流,艾邦特建有“储能产业交流群”,欢迎业内人员加入。
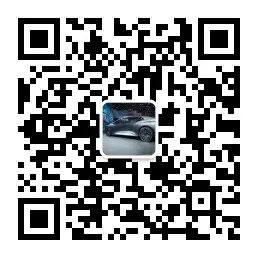
艾邦储能
更多储能资讯
扫码关注
原文始发于微信公众号(艾邦储能与充电):锂离子电池中废旧磷酸铁锂的回收方法