近年来复合材料的成型技术,为应对大型化和实现高速循环成型,以机械设备自动化为技术开发的主角。在大型化发展的风力发电叶片及开始用于主结构部件的飞机领域,为成型厚壁、各向异性的大型构件,自动铺层机的使用不可或缺;而在汽车部件等大批量生产中,没有材料搬运装置和自动成型机则难以实现。此时,为降低制造成本,许多研究致力于直接成型(Direct Forming),即不经预浸料或织物等中间基材,直接从线轴使用干纤维进行成型。
在直接成型中,纤维/树脂的一体化即浸渍工序需当场完成,因此流动性和浸渍性也成为树脂特性的重要指标。此外,如何将高速循环成型所必需的高反应活性树脂引入成型工艺、构建与树脂固化聚合反应相匹配的自动化/系统化,以及反过来改进或赋予适应成型工艺和装置的树脂特性,都是亟待解决的问题。
如上所述,为同时实现近年来的大型化/高速循环化和低成本化,关键在于实现成型工艺自动化与树脂成型特性的匹配,即所谓的从材料到制造的全局优化。当然,根据应用领域和规格要求等产品的各自特点,材料、工艺、装置的最优组合并非唯一,为实现正确的选择和匹配,正确理解多种多样成型技术各自的优缺点至关重要。
因此,本文将从材料成型特性与制造工艺匹配化举措的角度,概述近年来所研究的成型技术。
1、 树脂流动浸渍成型技术
在成型工艺中,将液态树脂浸渍到干纤维上的成型法是基本的成型方法,如手糊法等至今仍被广泛使用。此类方法可削减预浸料等中间基材的加工成本,并且通过利用铺放、三维编织、缝合等纺织技术改善机械性能,以及通过预制体加工工序的流水线化提高生产效率等,具有诸多优点。
1-1 VARTM成型中的树脂流动
使用开放式模具和真空袋的VARTM成型法(真空辅助树脂传递模塑),因其模具成本和设备相对简便却能高效成型高纤维体积分数(VF)的厚壁部件,已成为风力发电叶片、船舶等大型部件成型的主流方法。
VARTM成型法最初的课题是应对大型化。纤维中的树脂流动遵循达西经验定律。如图1所示,当树脂单向流动时,达西定律如式(1)所示。
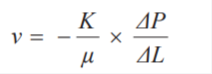
式中,v为树脂浸渍速度,K为纤维中的渗透率,μ为树脂粘度,ΔP / ΔL为单位长度的压力梯度。由公式可知,在促进树脂流动的压力梯度条件下,K值小的致密纤维或高粘度树脂会使浸渍速度ν变慢。
树脂供给压力ΔP 是真空泵侧压力与大气压之差,最大仅为1个大气压,随着浸渍进行树脂流动距离L增大,ΔP / ΔL减小,树脂浸渍速度ν会不断下降。由于树脂在固化前的可使用时间限制了可成型的部件尺寸,因此采用的方法是从多个位置注入树脂,或根据树脂浸渍情况依次切换注入位置,将树脂流动距离保持在某个值以下。
由于树脂流动过程中袋内压力在模具内并非恒定,在开放式模具成型中,靠近树脂供给侧的袋厚度(成型后板厚)会比真空泵侧增厚,导致部件内部VF不均匀。为此,开发并实用化了称为SCRIMP法的技术,即在层合材料上叠加一层渗透率大的流动介质层(称为流动介质)。如图2所示,这是一种利用流动阻力小的介质层来确保大浸渍距离的技术。但通常厚度方向的流动阻力比面内方向大得多,因此在成型厚壁、多层材料时,需注意靠近模具一侧出现干斑(Dry Spot)。作为参考,在泡沫芯材夹层板成型中,多采用称为芯材注入法(Core Infusion)的成型方法,即在芯材表面开设狭缝作为树脂流动路径。此狭缝在芯材两面呈网格状排布,并通过贯穿表里的孔洞,可同时浸渍芯材两侧的层合面。
采用双真空袋结构(叠加真空袋)的VaRTM成型法。通过外侧的袋和半透膜,可在成型部件全面施加真空压力,并且树脂流动后残留的微孔也可脱气,因此据称可降低孔隙率并确保均匀且高的VF。
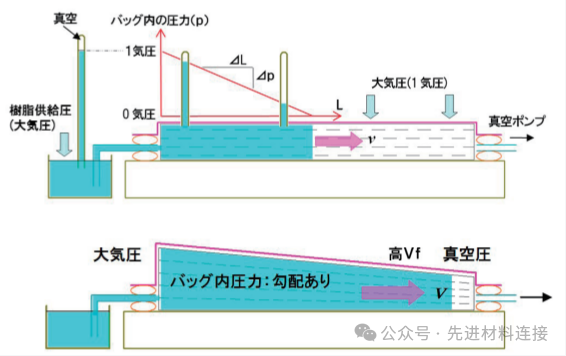
[图1 VaRTM浸渍中的袋内压力与VF]
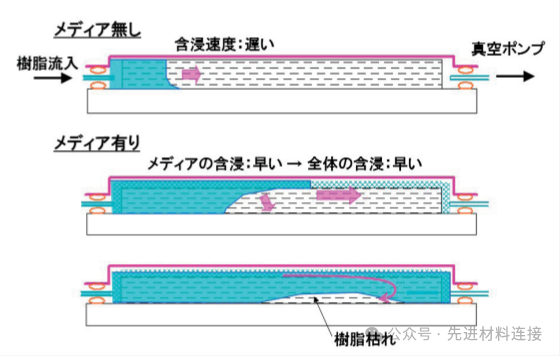
[图2 利用介质的树脂浸渍状况]
(上:真空袋结构;下:半透膜的作用)
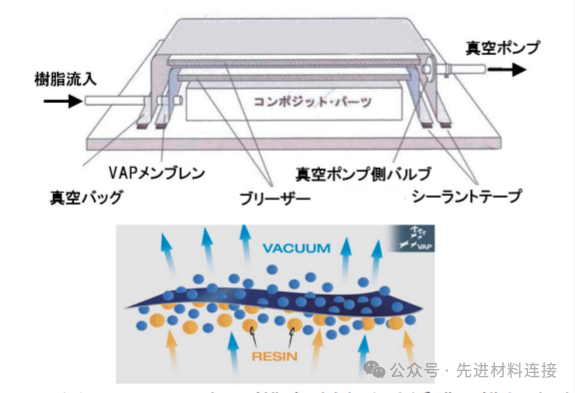
[图3 VAP法装袋结构]
波音公司的CAPRI法(受控大气树脂注入工艺,图4),是一种将图1中树脂罐液面所受压力降至低于大气压的方法。尽管预制体承受着完整的大气压,但由于浸渍过程中袋内压力被协调,树脂浸渍后仍能维持相当于施加在树脂罐上的减压量的压力作用于层合部件整体。结果使得获得高VF且均匀的板厚成为可能。
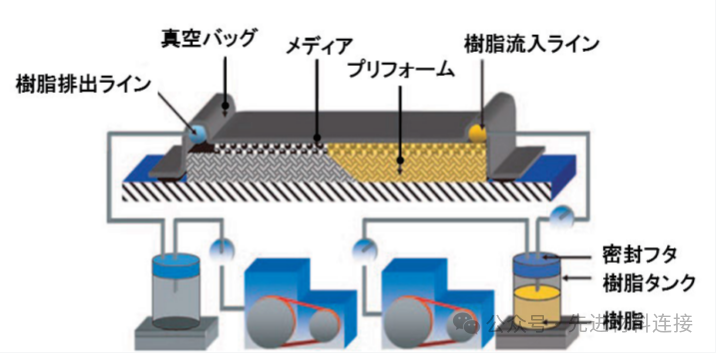
[图4 CAPRI法的装袋结构]
图5是在模具面侧设置树脂供给用流动介质的示例。干纤维内的树脂浸渍仅需板厚方向的距离,这点与SCRIMP成型法相同,但通过合理的装袋设计,可在成型部件几乎整个表面与模具面侧的介质层之间获得厚度方向(Z方向)的大压力梯度ΔP / ΔZ,因此即使是高粘度树脂也可实现VaRTM成型,该技术正作为飞机部件OOA(非热压罐)成型法之一推进实用化。
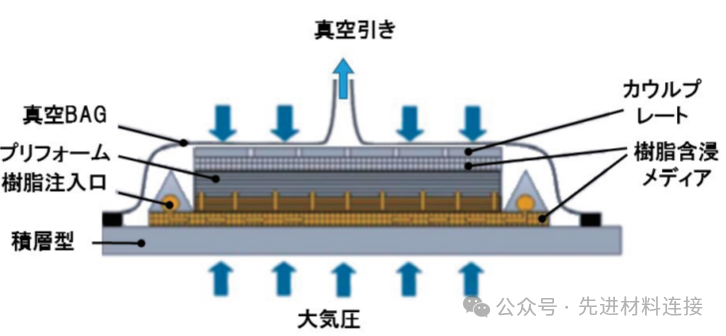
[图5 VaRTM成型法用于OOA成型的示例]
1-2 CFRP的VaRTM成型技术
采用VaRTM成型法成型CFRP时,由于纤维直径细导致树脂流动阻力大,且目视确认未浸渍区域困难。此外,纤维易弯曲导致刚性/强度的显现率低也是课题。在海上发电等大型化发展的风力发电叶片领域,为抑制叶片变形,碳纤维(CF)的使用不可避免,为此通过将预先拉挤成型的CFRP梁部件组装到叶片梁腹(Spar)部位,实现了使用纤维排列整齐的高品质CFRP。
在航空领域,要求更高的成型质量和机械性能,因此挑战在于如何在使用强度、韧性优异的高粘度树脂的同时,在部件内部实现均匀且高VF的浸渍。EADS-Scartex公司开发的VAP法(真空辅助工艺,图3),使用具有透气性的半透性膜材进行装袋,其外侧再叠加常规的真空袋。如果部件尺寸允许使用热压罐,则可在VARTM成型法的开放式模具中进行树脂加压注入。图6是SLI成型法(单线注入)的系统构成。通过热压罐对真空袋面加压,可在低于罐内压力的压力下进行树脂加压注入(RTM)。此法不仅适用于VARTM法难以使用的高粘度树脂,而且无需介质即可实现单点树脂注入。
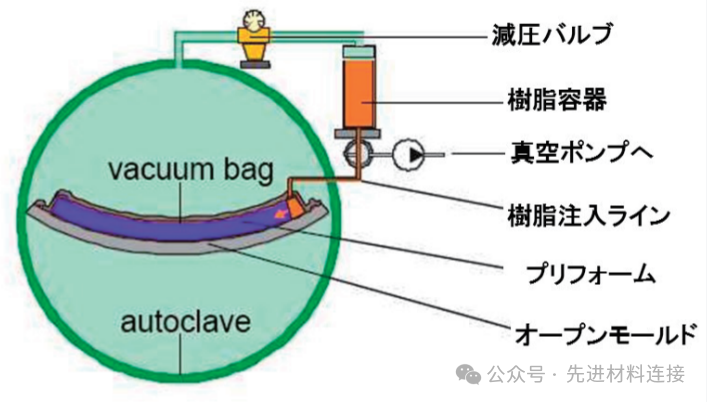
[图6 SLI成型法的系统构成]
(标注:阀门、树脂容器、接真空泵、树脂注入管线、预制体、开放式模具)
1-3 HP-RTM成型技术
汽车部件,尤其是量产车用复合材料的应用,必须同时实现高速循环成型和低成本化。图7是Krauss Maffei公司HP-RTM(高压RTM)成型系统的示例。如图所示,该系统由两阶段构成:预制体工序——将具有优异铺覆性的NCF材(无屈曲织物,或称MA材:多轴向织物)按样板裁切,使用粘合纤维(Tackifier)通过加热压机成型预制体;以及RTM工序——由合模机和树脂注射机完成。此时,通过耐压泵以超高速流在即将进入模具前使树脂(主剂与固化剂)撞击混合,并混入脱模剂,从而可省略脱模后的清模和离型处理。通过利用物料搬运(Mat-Han)机器人自动执行各工艺的材料搬运,可实现几乎仅含成型工序节拍时间(Takt Time)的连续生产。特别是在HP-RTM成型法中,通过使用称为“Snap-Cure”(快速固化)型、适用期(Pot Life)2分钟以下的超高速固化型树脂,实现了高速循环成型。
图8所示的湿法模压成型法(Wet Press Molding),通过取消抽真空工序并缩短树脂注入时间,实现了更短的成型周期。此成型法最初旨在利用因将NCF材裁切成样板形状而产生的边角料。将回收的边角料经裁切、梳理(Carding)等回收处理后制成的毡材置于压模中,涂布定量树脂,在压制工序中完成浸渍与固化。其工艺与传统的冷压法基本相同,但采用了HP-RTM成型法中实用化的Snap-Cure树脂,实现了高速循环成型。
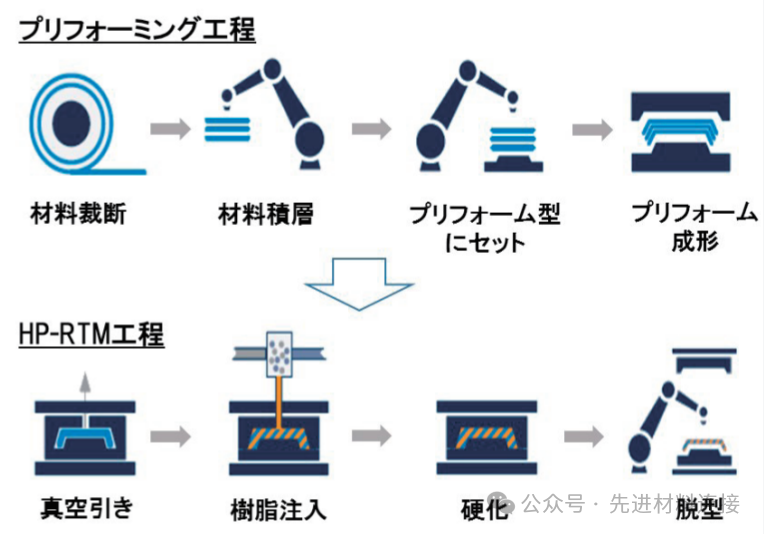
[图7 HP-RTM成型系统]
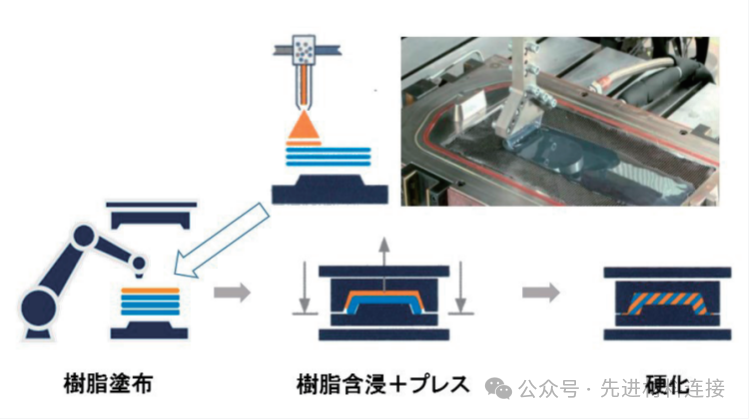
[图8 湿法模压成型工艺]
1-4 干纤维的应用技术
为将干纤维应用于飞机部件,正在开发可适用于ATP设备(自动铺带机)的UD(单向)带材。这不仅是为了削减预浸料带的加工成本,更是以提高整个成型过程的效率为目标。HEXCEL公司开发的Hi-Tape(图9),在碳纤维(CF)两侧附着有热塑性薄层毡材作为粘合剂,可通过加热加压辊在ATP设备上进行自动铺层。因为是干态带材,材料储存和操作简便,且铺覆性良好,因此可比预浸料ATP设备大幅提高铺层速度。使用预浸料UD带材的ATP设备铺层时,为适应三维形状,有时也使用6mm左右的窄幅带材,带间间隙(间隙或重叠)的管理成为课题,而比预浸料铺覆性更佳的干纤维在此方面具有优势。图10是正推进在主结构上实用化的加强壁板示例。通常,桁条材是将所需数量的预制体(Prepreg Layup?)铺在平板上后弯曲成所需形状进行铺层,但使用预浸料时,层间粘性会导致皱褶或弯折,甚至在热压罐固化过程中,树脂软化也可能在拐角处产生纤维排列不整。在图中的示例中,由于外蒙皮(Skin)与桁条通过VARTM一体成型,因此获得了良好的成型品质。
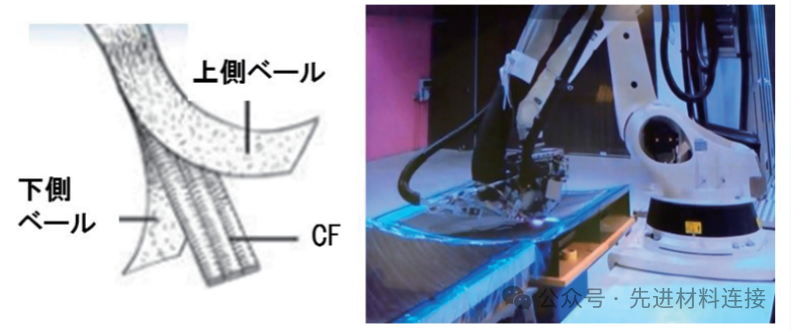
[图9 干纤维带材(Hi-Tape)与ATP设备]
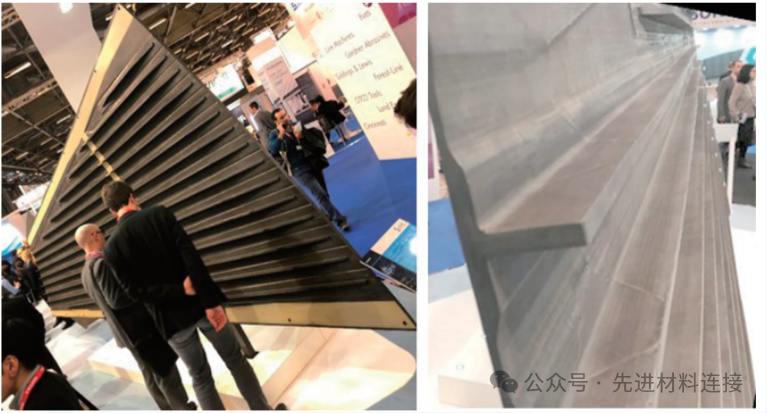
[图10 利用干纤维带材VaRTM成型的加强壁板]
(HP-RTM成型示例)
图11是用于RTM成型的预制体材的示例,由薄层UD带材经裁切成一定长度后通过粘合剂随机成毡(Sheet)制成。若能按近净形(Near-net shape)成毡,可大幅提高材料利用率。由于是以UD带材为基材,通过加热、加压利用带间滑动可轻松进行预制体加工,具有良好的易加工性,并能获得与连续纤维ISO(等方向)层合材同等的物性,是一种具有优异材料特性的基材。
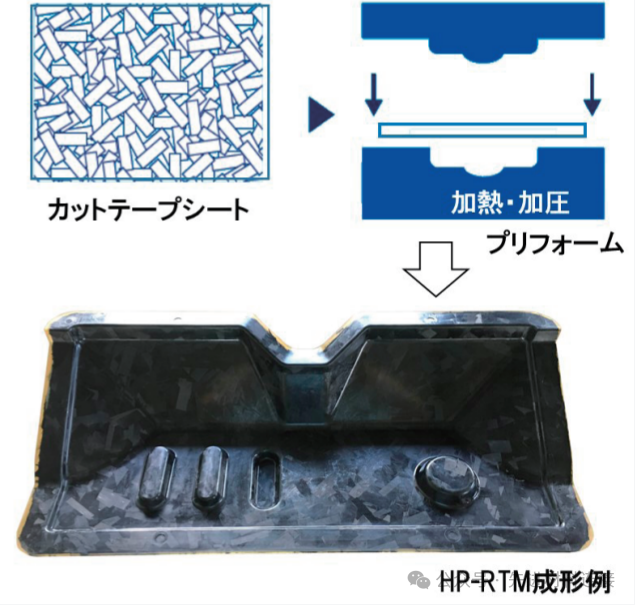
[图11 HP-RTM成型]
2、 伴随材料流动的成型技术
使用模具和压机的对模成型(Matched Die Molding)技术是近年来取得巨大发展的成型技术之一,多种多样的材料与成型法的组合正面向实用化开发中。
对模成型法不同于注塑或传递成型那样在预先闭合的闭式模具内压入材料,而是利用压机的合模工序对材料进行加压、赋形、固化/硬化,因此材料流动距离短,能够使用长纤维、高VF材料,适合于要求更高机械性能的部件成型。如今,伴随着新型热塑性树脂复合材料的开发以及模具/压机技术的发展,该技术正为超高速循环成型的实现而积极开发中。
2-1 使用长纤维的热塑性树脂复合材料
热塑性树脂复合材料具有诸多卓越特性:无需硬化/聚合反应,通过加热软化与冷却固化即可实现超高速成型,甚至可熔融焊接,且回收性高。
其中,以热塑性树脂为基体加工而成的片材进行的压制成型,可实现与钣金冲压相当的极短时间成型,因此称为冲压成型法(Stamp Forming)。以汽车部件应用为目标,结合了物料搬运(Mat-Han)等周边设备技术的自动化制造技术正被研究。
冲压成型可根据片材的纤维长度、织物形态进行加筋(Rib)或厚度变化,还能与注塑成型组合实现复合(Hybrid)成型等,有望实现多样化的成型。图12是易加工性热塑性片材的开发示例,通过CF毡或如图11所示的CF-UD裁切带制成的片材,兼具织物基材无法实现的复杂形状成型性和高机械性能。图13是LFT-D(长纤维热塑性直接)成型法的开发示例,是从线轴直接将CF导入混炼机,将称为“股料”(Fitton)的熔融态热塑性树脂复合材料直接进行冲压成型的工艺,是追求低成本化的过程。
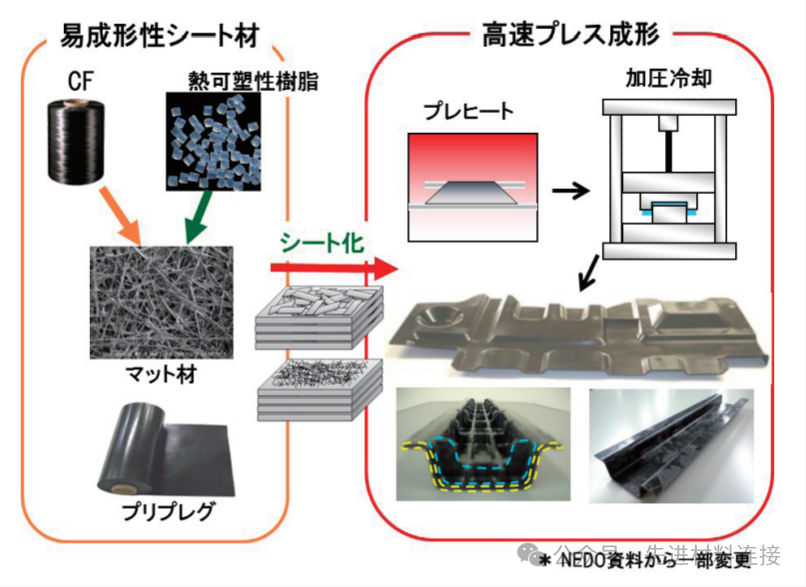
[图12 热塑性复合材料片材与压制成型]
(高速压制成型、高温压制成型、预热、毡材、预浸料)
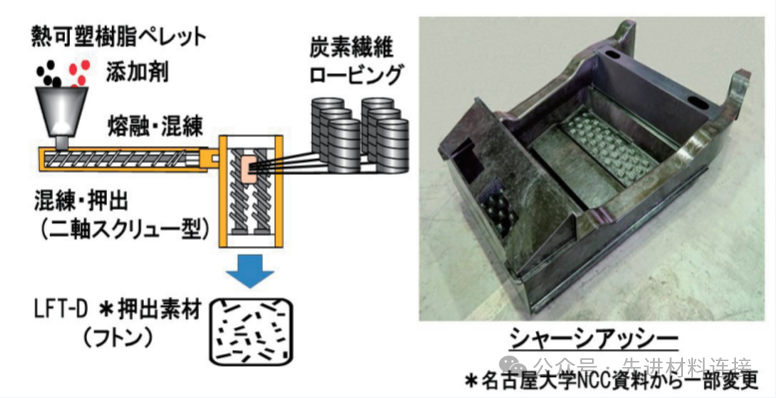
[图13 LFT-D材制造工程与试制示例]
2-2 热塑性树脂复合材料的冲压成型
冲压成型需留意的是模内材料流动和冷却固化时的压力管理。与热固性SMC材的压制成型不同,在边赋形边同时进行冷却固化的冲压成型中,伴随合模的材料流动时间在1秒以下,此期间材料流动性随冷却急剧下降。为在确保赋形性的同时尽快冷却固化以缩短周期时间(满足这相互矛盾的条件),需要采用将材料加热至不产生热劣化的尽可能高的温度,并在较低温的模具中短时间合模的工艺。此外,此合模需要数MPa至10MPa以上的高模面压力,以实现材料流动和赋形。这与在1MPa以下压力成型的预浸料成型大不相同。但重要的是,在冷却固化过程中也需一直维持此加压状态,这不仅关乎表面品质,更是确保材料强度等机械性能的关键。这是因为树脂的熔融温度即成型温度通常高于热固性树脂的固化温度,且冷却过程中材料的收缩量大。
在冲压成型中,与利用塑性变形的钣金冲压不同,宏观上加工过程中的纤维长度不变,赋形是通过熔融树脂伴随发生的纤维弯曲和取向变化、层间/带间的滑动和移动等实现的。因此需要采取避免弯折和皱褶的措施(参见图14,15)。连续纤维或织物层合片材的压制成型中,可采用侧面开放型(Side Open)模具,通过保持模具外部的材料来促进层间滑动。这也是从预热到脱模的物料搬运(Mat-Han)中的有效手段。对于非连续纤维材料的成型,则需要采用剪切边型(Shear Edge)模具来防止模内材料流出。
如上所述,为在冷却固化结束前持续对材料施加合模力,上下模并非完全密合,而是通过液压等压力控制进行合模。也就是说,成型品的肉厚由材料投入量决定,因此控制下死点位置的钣金用压机无法用于冲压成型。为此开发了专用压机,能在加热材料冷却前高速合模,并满足上下模的平衡度要求。图16是具备上下台面间合模高度(Shut Height)高速移动和合模控制两种机构,并通过四轴独立执行器维持高台面平衡度的压机示例。
[图14 片材的层间滑动加工]
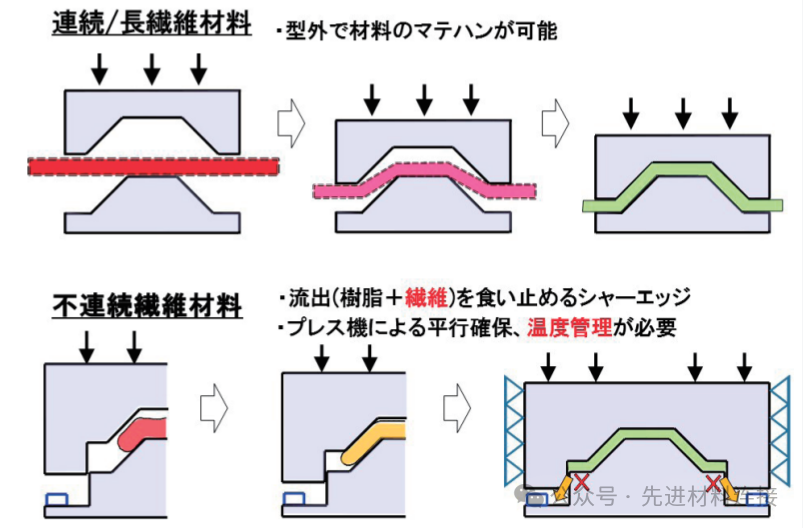
[图15 冲压成型与模具形状]
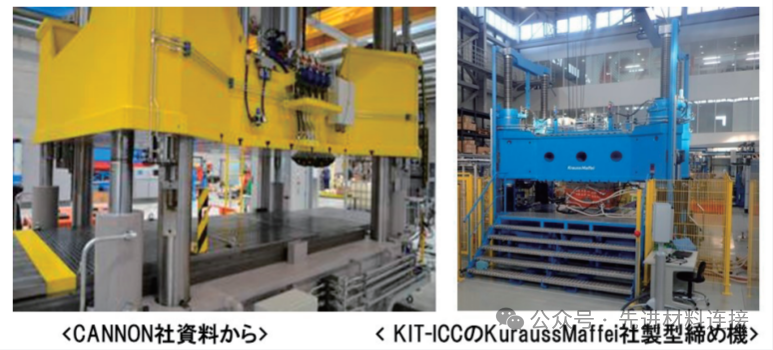
[图16 冲压成型用压力控制压机示例]
3、 高速成型与模具技术
缩短成型周期时,成型工艺成为伴随材料流动及压力/温度急剧变化等非稳态、随时间变化的动态过程。对于Snap-Cure树脂或热塑性树脂等,超短时间内发生的聚合、硬化或固化反应与成型中的材料流动及压力变化相互影响,呈现非线性且相互耦合的行为。
3-1 RTM工艺的树脂流动与压力管理
图17示意性比较了VaRTM成型法与HP-RTM成型法工艺过程中模内压力的变化。图中从左至右表示树脂流动浸渍时,各时刻模内成型面的压力分布(上图)及各位置压力随时间的变化(下图)。
在HP-RTM成型法中,由于是定量泵注入树脂,随着树脂浸渍长度增长,模内压力会逐渐增大。若渗透率大或树脂粘度小,在VaRTM成型法中树脂流动速度会增加,但在HP-RTM成型法中模内压力仅会降低,树脂流动速度不变。树脂注入结束时,两种成型法的模内压力均非恒定,但在HP-RTM成型法中,模内树脂填充完毕的瞬间即转为静压状态,整个模内压力上升至注入泵的设定压力。模内的高压状态是成型无微孔且具有高机械性能和表面品质部件的关键条件,这与热压罐加压固化预浸料的机制相同。
顺便提及,在使用模具的闭式模具成型的HP-RTM成型法中,成型品各部位的VF由模具形状和投入的预制体的纤维量决定,因此不会产生VF不均匀。
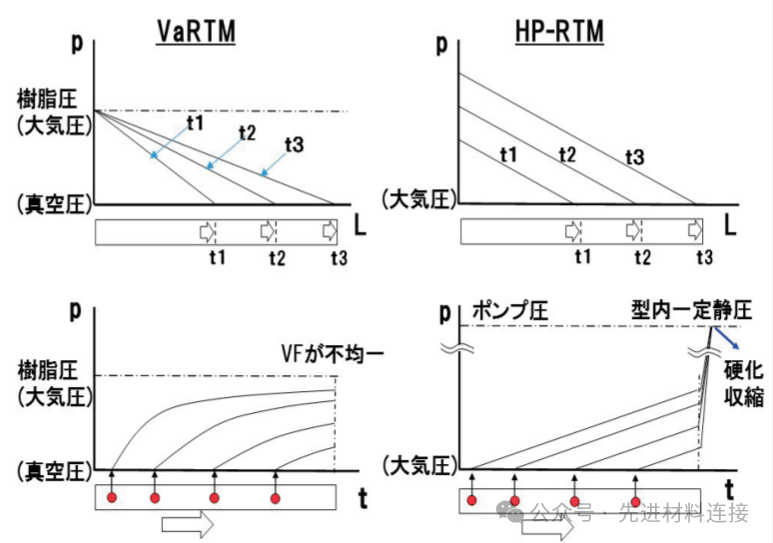
[图17 伴随树脂流动的模内压力]
3-2 适应各成型工艺的模具技术
近年来复合材料成型技术的发展,很大程度上得益于模具应用的普及。在树脂聚合/硬化或固化与材料流动、压力变化相互耦合的动态非线性成型过程中,作为高再现性即低不良率成型法成立的首要要素技术就是模具。
使用模具和压机的成型法,比热压罐成型法或VARTM成型法等开放式模具与真空袋的组合,能期待高得多的形状再现性。然而,与能在成型部件全面施加均匀压力的柔性真空袋不同,对于坚硬的金属模具,若无伴随模具尺寸精度、温度调节、合模力等的高精度工艺管理,成型本身甚至难以成立。也就是说,称模具技术本身就是成型技术也毫不为过。
在SMC材的压制成型中,投入调温至硬化温度的模具内的材料,通过载荷控制型压机加压/加热,在流动的同时完成赋形。升温后低粘度的树脂会从加工出约0.1mm间隙的模具剪切边(Shear Edge)部微量流出,而增强纤维则留在模内,伴随着硬化反应引起的凝胶化,作用于材料的加压力得以维持,同时合模继续进行。为应对这种相互耦合的行为,实现成型品表面品质与机械性能的双赢,需进行优化:根据树脂硬化速度设定模具温度、平衡型腔间隙和流动阻力的合模力、根据型腔间隙流出量增减材料投入量等。
图15所示的非连续纤维材料冲压成型中,为完全阻止材料流出,剪切边部的间隙需在0.05mm以下,需要高精度的模具加工技术。
在HP-RTM成型中,如图17所示,注入模内的树脂压力也影响成型品的机械性能和表面品质。对于约10MPa的高注入压力,低粘度的RTM成型用树脂无法通过剪切边抑制流出,因此需要密封垫(Packing)等密封材料。此密封机构也是在合模后树脂注入开始前模内真空脱气工序所需的功能,是RTM成型模具的特征。
4、 总结
近年来复合材料的应用扩大,很大程度上归功于针对各种应用对象优化的成型工艺的多样化及其进步。在迎来应用扩展期的当下,以实现自动化为重点的装置技术开发备受重视,成型技术正逐渐被纳入零件/商品的制造流程中作为单纯的一道工序。
在动态非线性的短时间成型过程中,为获得高成型品质,材料流动和压力管理是关键,因此推动了模具和压机的应用。在此期间,可以说材料本身也从成型特性与制造工艺匹配化这一全局优化的角度,以更廉价、更快、更易制造为目标进行了改进开发,其目标甚至优先于提高成型品机械性能。
来源:先进材料连接