CCS集成母排主要由信号采集组件、塑胶结构件、铜铝排等组成,通过热压合或铆接等工艺连接成一个整体,应用于新能源汽车、储能电池模组内,实现电芯高压串并联以及电池的温度采样、电芯电压采样功能,并通过信息采样组件与连接器将温度和电压等信息传输至BMS系统,属于BMS系统的一部分。
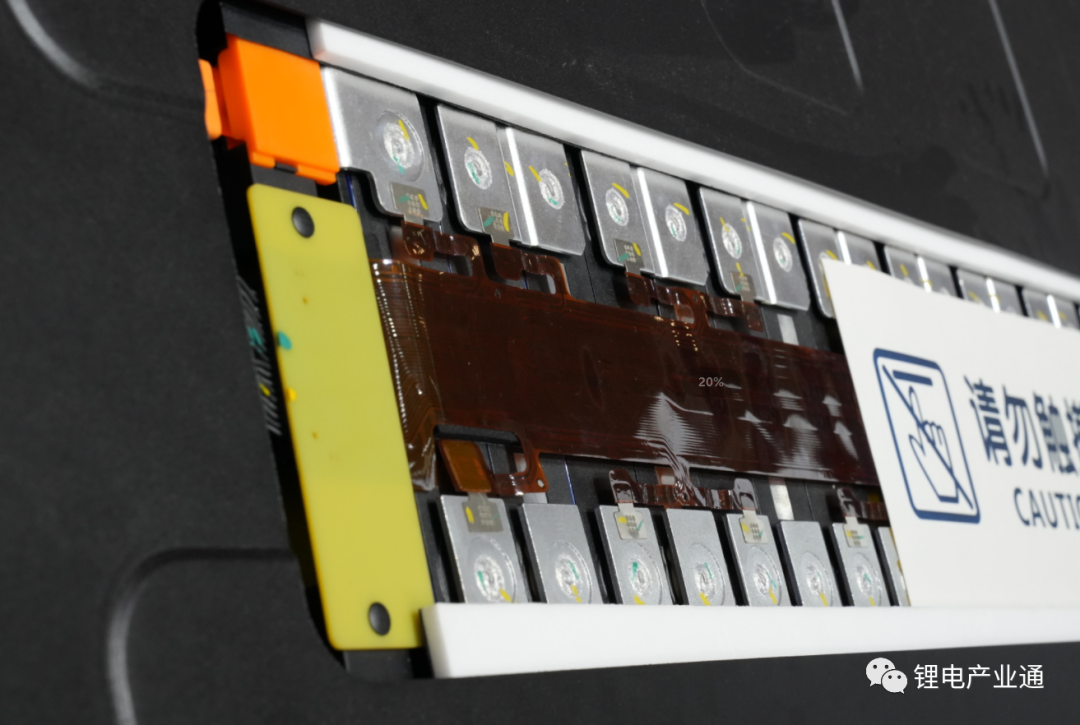
图 轻卡标准箱,摄自CIBF2023中创新航展台
作为电池pack/模组内部重要的电连接组件,不同的电芯成组方式,电池包标定参数,使用环境,以及对电池包内部空间、重量等的要求,都会对CCS集成母排的采样组件、生产工艺、材质选择等有不同的要求。因此,为了满足应用端多样性的需求,CCS产品也在不断升级信号采集组件、优化集成工艺等,发展出了多种技术路线,包括线束、PCB、FPC、FFC、FDC等多种采样方案,以及注塑支架、拼接、PET热压膜、吸塑隔离板等多种集成方案。
此前,我们简单介绍过 CCS集成母排技术路线 以及 采集组件 。今天,我们来看一下CCS的集成方案。
一、注塑支架+铆接工艺
在行业发展初期,CCS产品主要采用注塑支架的集成方案,通过热铆或者卡扣固定支架、信号采集组件及铜铝排等。
图 采用注塑支架+热铆工艺的线束CCS,摄自CIBF2023硅翔展台
注塑支架通常采用阻燃PC+ABS或PA66注塑而成,塑件需要通过内应力、双85、高低温冲击等测试,具有机械强度牢固,结构强度好、工艺成熟稳定等优点。
不过,由于注塑支架厚度较厚,且重量相对较重,会在一定程度上影响动力电池内部空间利用率及续航里程的提升。此外,注塑支架尺寸受注塑机吨位限制,大尺寸CCS注塑支架,成型难度大,模具开发难度大、设备成本高等。因此,业内开发出了拼接隔离板方案,运用数块拼接支撑板替代一体注塑支架,以减少注塑工艺的难度和设备投资。
二、吸塑隔离板+热铆工艺
CCS吸塑隔离板使用阻燃PC薄膜吸塑、裁切成型,通过热铆工艺与信号采集组件、铝巴连接整合成一个整体。
采用更为轻薄的吸塑隔离板替代注塑支架,可以有效降低重量,提高电池包空间利用率,且吸塑成型模具费用低,专用设备投入少,生产效率高,灵活性高,具有一定的成本优势。
但是,吸塑产品比较薄,承重能力相对较差,同时也可能存在涨缩、尺寸偏差大等问题。
三、热压绝缘膜集成
CCS集成母排热压工艺是使用 PET绝缘膜替代传统隔离板,经加热粘合将铝巴及信号采集组件等组件压合成一块薄片,可以有效减小产品体积、重量以及减少配件数量,使CCS集成母排结构更加轻薄、规整,集成度高,密封绝缘可靠,可实现自动化装配,有助于提升电池模组的空间利用率和生产效率,符合行业轻量化、集成化以及大模组的发展趋势,近年来得到较快发展。
图 CCS集成母排热压工艺流程,截取自西典新能招股书
与注塑、拼接方案结构相比,热压CCS更加轻薄,与吸塑方案相比,热压CCS产品完全集成化,稳固性更高。不过,热压工艺也存在设备投入大,热压时间长,生产效率较低,总体成本较高等问题。
图 热压CCS,摄自CIBF2023 湖北永创鑫展台
四、平板结构+铆接
除了上述目前应用较多的集成方案外,行业内也推出了一些新的技术来进一步降低成本。例如,瑞浦兰钧在2022年9月申请的相关专利中提到的平板结构:CCS集成母排采用平面板体结构的绝缘支撑板,利用铆钉连接方式,连接固定绝缘支撑板、信号采集组件、铝巴。相比注塑/吸塑/热压的集成方案,可以进一步降低集成母排的生产成本。
当然这种结构并不一定适合新能源汽车动力电池需要经受频繁的颠簸和振动的使用环境,而是更适用于室内储能这类不需移动的使用场景。
具体工艺细节可以查阅专利文本,而采用平板结构/铆接工艺的产品也有在此前的展会中展出过。
总体来说,CCS集成母排的不同集成工艺各有优势,终端可以根据不同应用需求选择最适配的方案。
注:本文内容通过群友交流、搜集网络信息整理,如有错漏,欢迎添加管理员微信指正,感谢!
原文始发于微信公众号(艾邦高分子):CCS集成母排4种集成工艺简介