气味,既是一种感官体验,也是一种质量认知。在密闭的汽车座舱内,塑料带来的“新车味”并非高端象征,反而可能成为消费者投诉的焦点。小编结合工程实践,系统梳理气味的来源、机理、分析方法与材料工程师可施加的控制策略,帮助汽车内饰材料设计从源头降低气味风险。
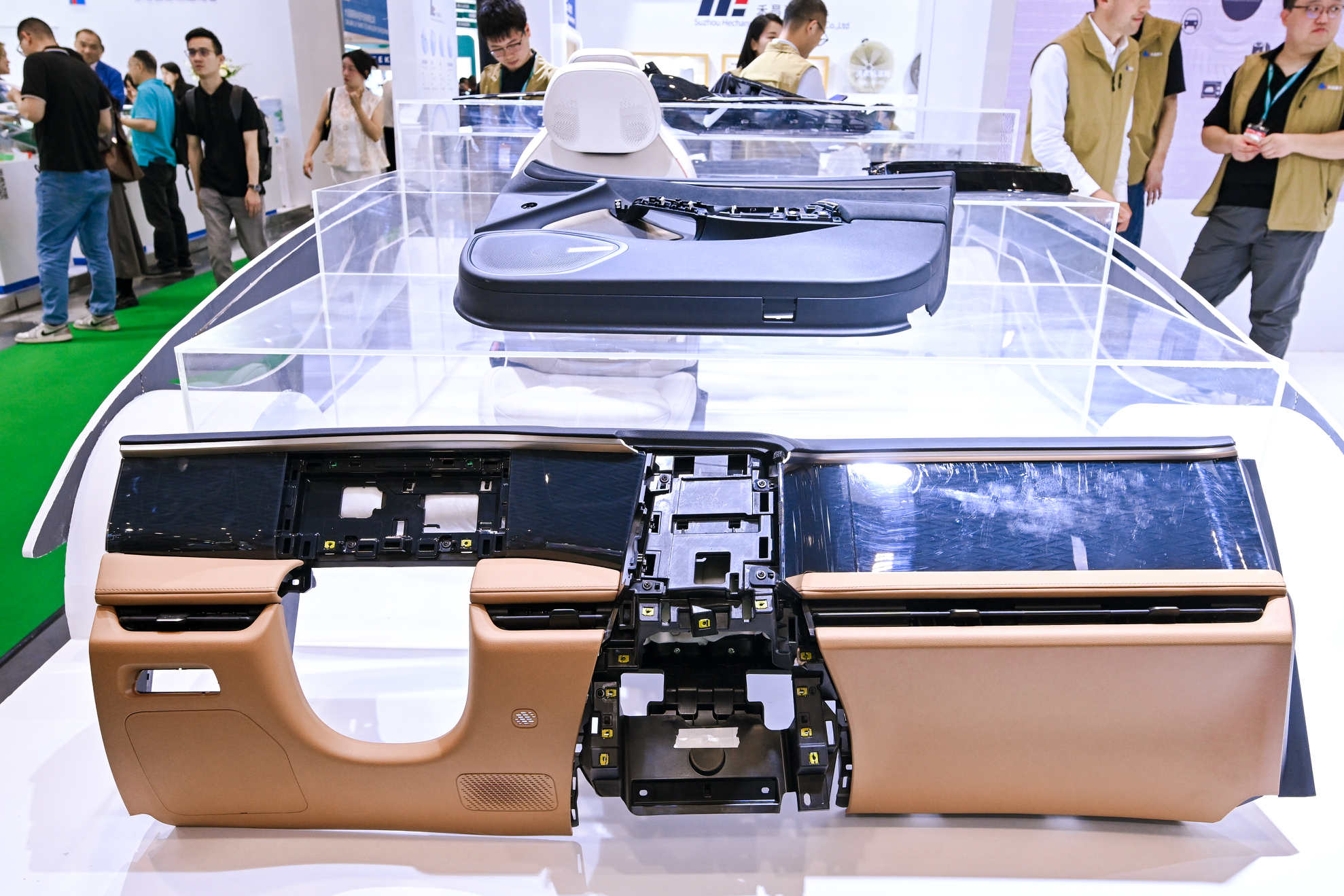
一、塑料气味是怎么来的?
塑料材料中的气味分子主要以挥发性有机化合物(VOCs)形式存在,它们通过以下三种机制释放到空气中:
1. 扩散(Diffusion):材料内部未反应单体、小分子向表面迁移;
塑料中的 VOCs 遵循菲克第二定律向表面扩散。以聚丙烯(PP)为例,其内部醛类物质向表面的扩散系数约为 10⁻⁹cm²/s,在 23℃环境下,需 48 小时才能达到表面浓度平衡。而当温度升高至 60℃(车内夏季温度),扩散速率可提升 3-5 倍。
2. 解吸(Desorption):吸附在材料表面的气味分子释放到空气中;
3. 迁移(Migration):来自增塑剂、润滑剂、残留溶剂的迁移。
人体嗅觉的精密解码:从分子识别到神经传导
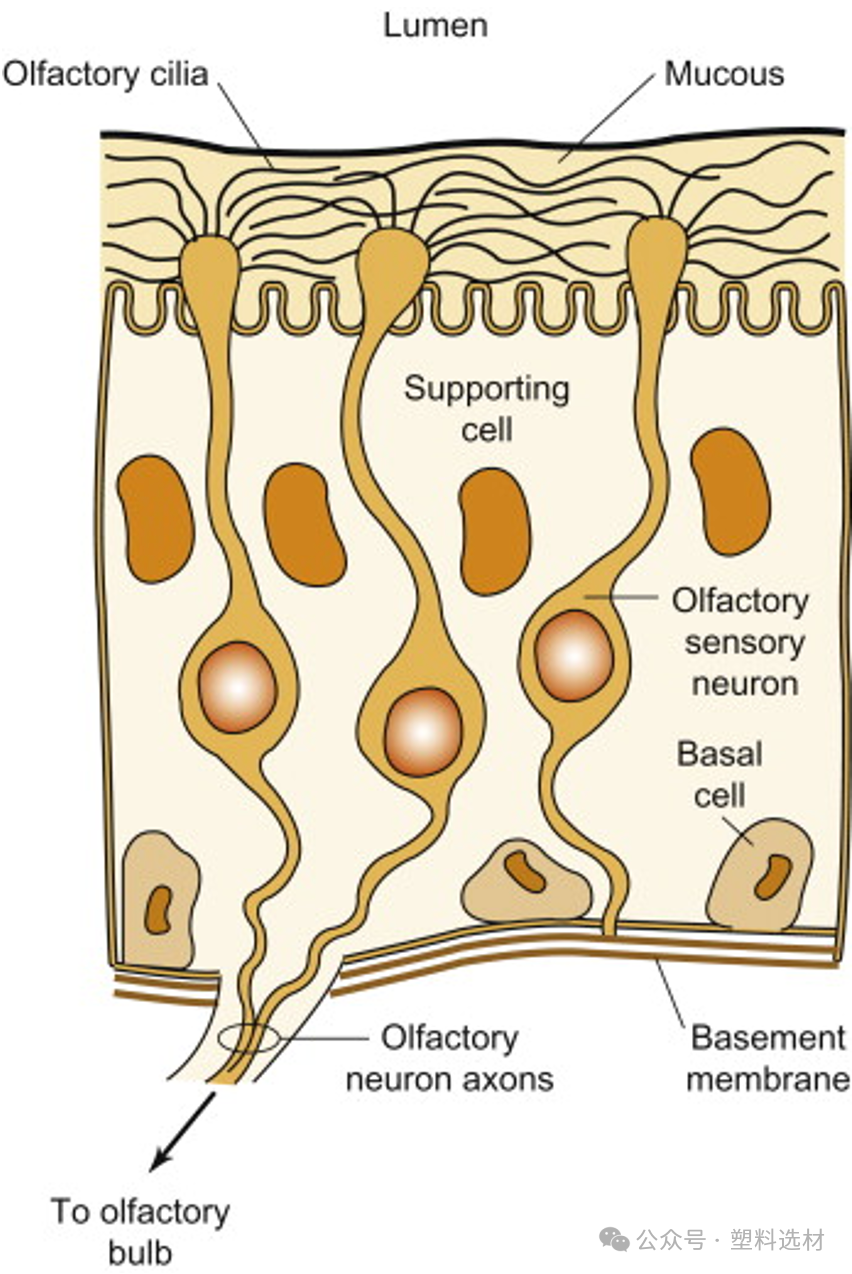
https://ars.els-cdn.com/content/image/3-s2.0-B9780123749475000523-f52-01-9780123749475.jpg
当塑料释放的挥发性分子(如壬醛、癸醛)进入鼻腔,一场发生在微米级空间的精密识别开始启动。嗅觉上皮层(约 5cm²)中密布着 350 种嗅觉受体蛋白,它们如同 "分子钥匙" 特异性识别气味物质。以 (E)-2 - 壬烯醛为例,其碳链结构与嗅觉受体 OR51E2 的结合能达 - 8.7kcal/mol,这种特异性结合引发离子通道开放,产生电信号。
嗅觉信号传导遵循 "锁钥模型":气味分子与纤毛上的 G 蛋白偶联受体结合后,通过 cAMP 第二信使系统使细胞膜去极化,电信号沿嗅神经纤维传至嗅球,经 mitral 细胞和 tufted 细胞处理后投射到大脑皮层。这一过程中,单个嗅觉神经元仅表达一种受体,却能通过组合编码识别上万种气味 —— 如同 PP 材料中的醛类混合物,会激活 OR1A2、OR2J3 等受体的组合响应。
这种生物识别机制为材料气味检测提供基准:当 PVC 人造革释放的 DEHP 浓度超过 2200μg/m³时,其分子与 OR3A4 受体的结合会触发 "刺激性" 嗅觉信号,这正是车内气味评估中需要规避的阈值。理解这种分子 - 受体的作用机理,能帮助选材工程师从 "人类嗅觉感知图谱" 反向设计低气味材料。
二、不同塑料的典型气味及来源
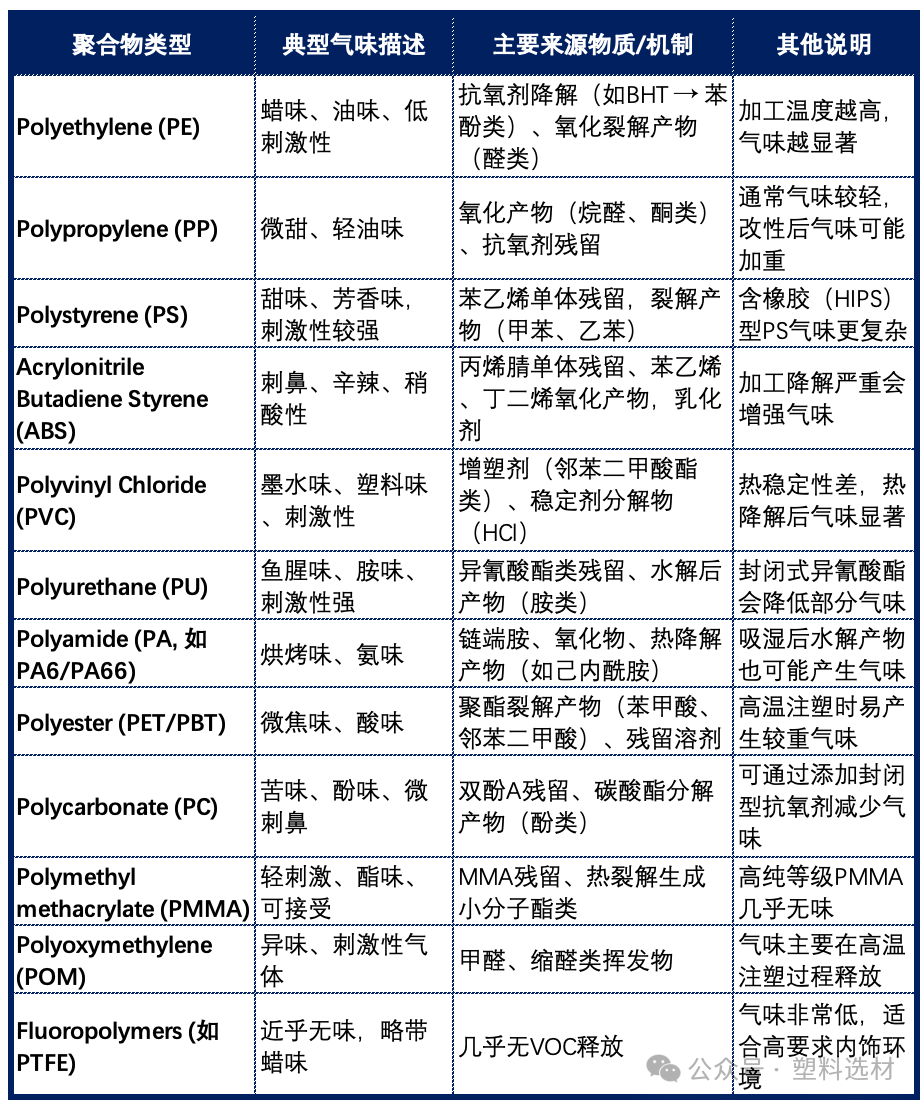
三、气味的形成机制
塑料材料的气味不是凭空而来,而是在加工、储存和使用过程中逐步“生成”的,主要机制包括:
- 热裂解:加工温度高导致分子断裂,形成低分子气味产物(如醛类)
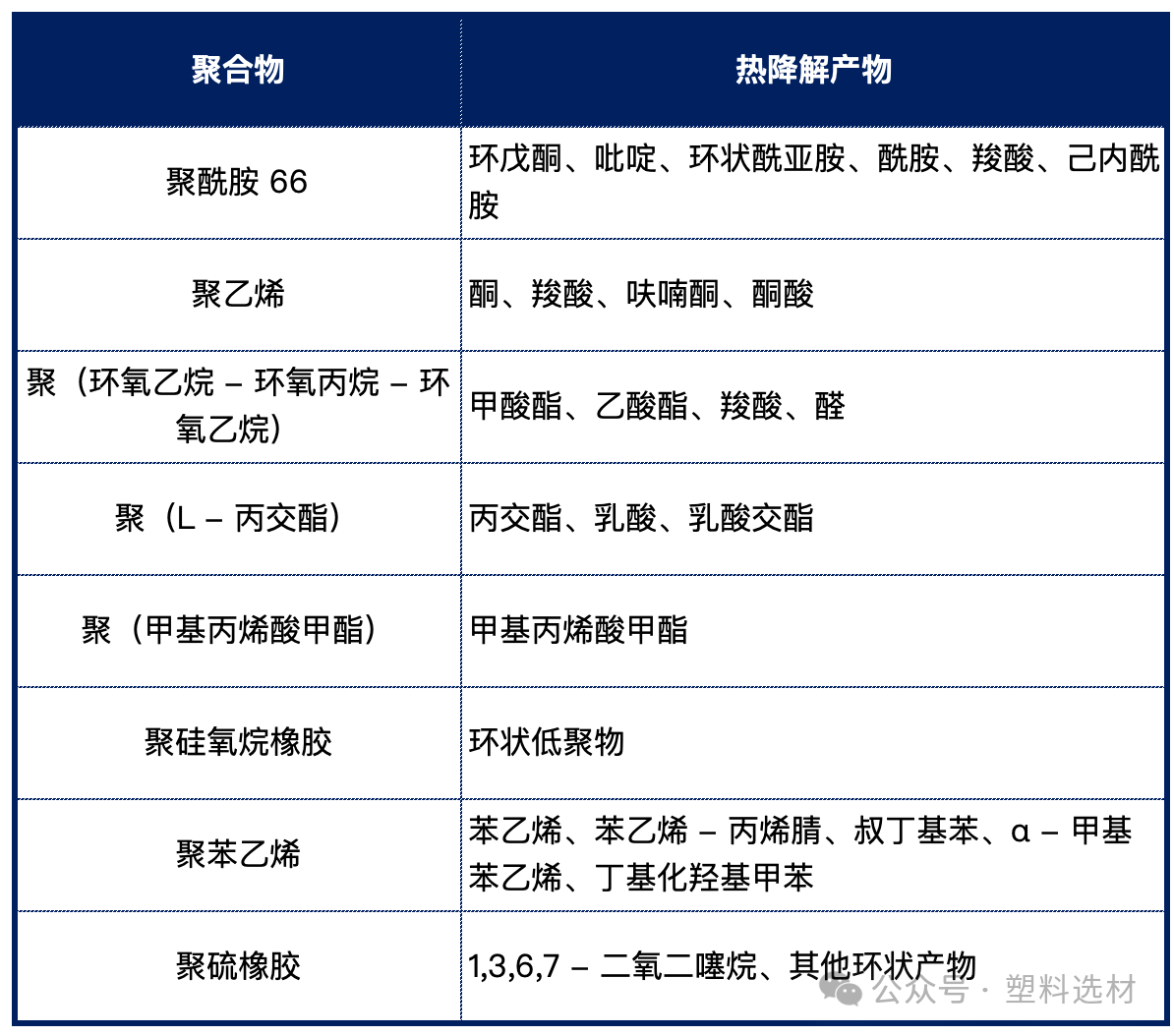
- 氧化降解:抗氧剂或聚合物氧化产生异味(例如BHT氧化物)
聚酰胺(PA66):热氧化降解产生的环戊酮类物质,如 2 - 乙基环戊酮,在 100℃老化 300 小时后浓度可达 0.3μg/g,形成 "药味"。
- 光老化:UV导致聚合物链断裂,释放小分子气体
- 加工残留:如催化剂、溶剂未除尽
聚氨酯(PU):胺类催化剂残留如三乙胺,其嗅觉阈值仅 0.67μg/m³,是 PU 泡沫 "鱼腥味" 的主要成因。
四、如何分析塑料气味?
塑料气味的测试与评价方法,常见包括:
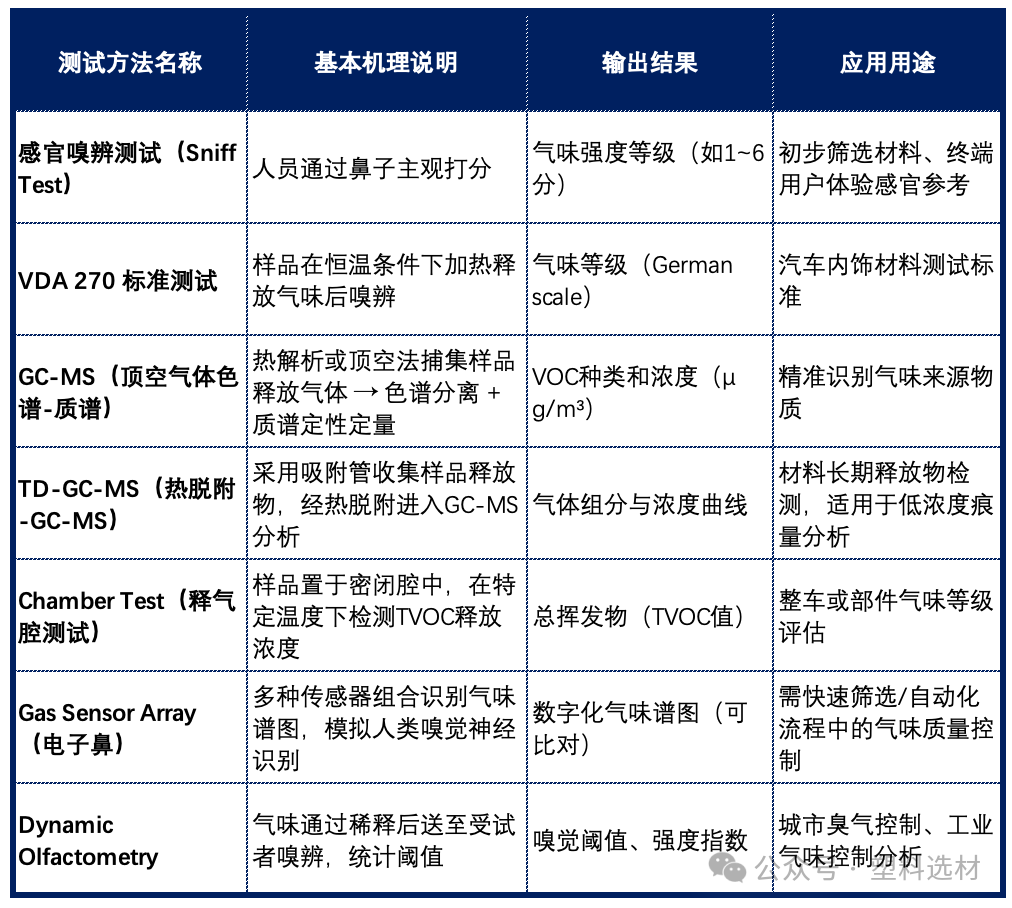
在选材初期控制气味,是成本最低、效果最显著的策略。建议如下:
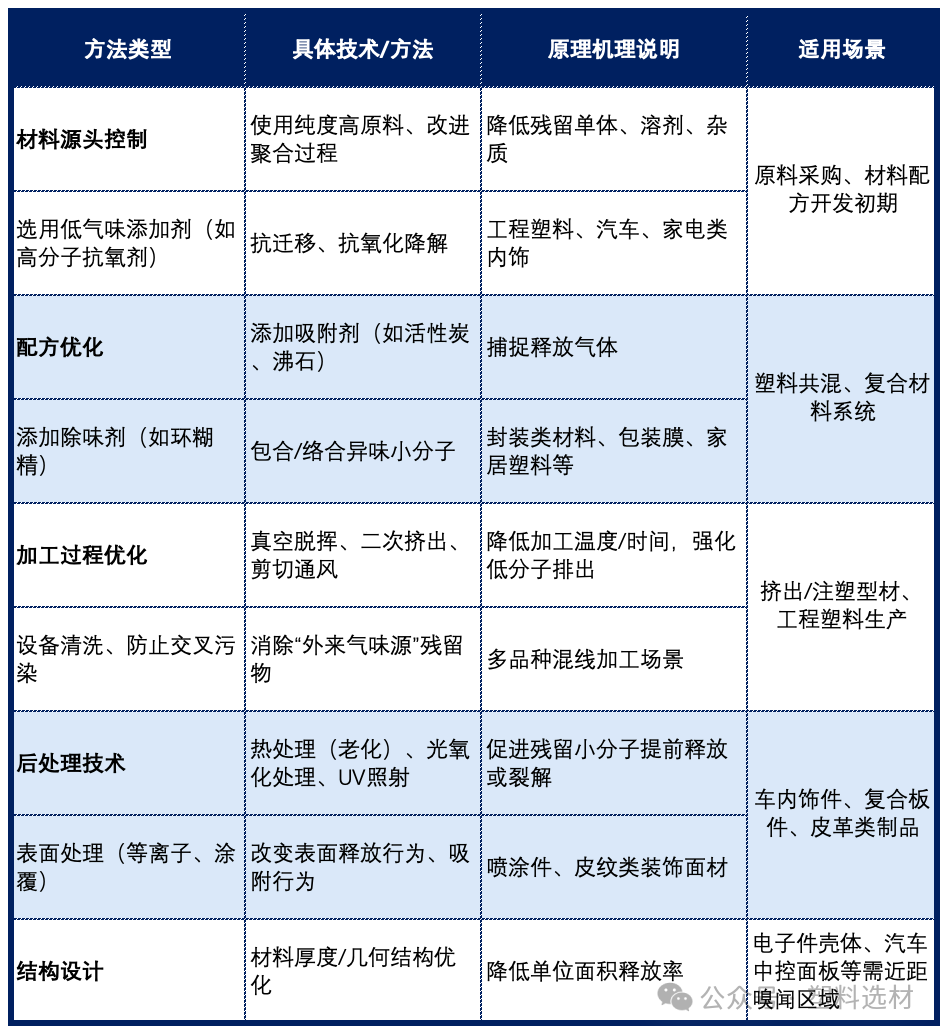
结语:从"嗅觉体验" 到 "分子设计" 的选材革命
汽车内饰的低气味化不是简单的感官优化,而是涉及聚合物化学、传质动力学、分析化学的系统工程。
对于选材工程师而言,需建立 "结构 - 性能 - 气味" 的关联认知:
当 PP 的分子链规整度提升 15%,其醛类释放量可降低 38%;
当 PVC 增塑剂的分子量从 300Da 提升至 500Da,迁移速率下降 60%。
这些基于分子层面的设计逻辑,正是突破低气味材料技术瓶颈的关键。
来源:塑料选材